你可以這樣做 - 幫助製造業AI導入降低失敗率,快速看見轉型成效
- 盤點現場設備與數據基礎,列出未達標項目不少於3處
補足硬體軟體落差,減少AI系統導入時的資訊斷層[2][3]
- 鎖定單一產線試點,每次優化不超過10%工序
循序漸進驗證效果,避免一次擴張造成資源浪費[1]
- 每月檢查模型表現並記錄異常率變動≥5%
及早發現模型失效或流程誤差,有利持續調整優化[2]
- *預留至少7天*為全員同步訓練,納入新舊員工意見
提升團隊認同感與操作熟練度,加速技術落地[1][3]
現場壓力不減,AI小規模試點怎麼贏得信任?
「我們剛要導入智能製造時,現場許多人其實感到壓力很大,」一位中型機械廠產線主管分享。唉,他說話的時候,其實手還在抖,「無論是資金投入還是流程變動,都讓大家有點排斥。」那個現場的氛圍……好像每個人都怕被問到意見,我突然想到上次開會也是這樣,但還是拉回正題。經過一輪訪談彙整後,大致可以發現,只要初期直接大規模導入人工智慧技術(像什麼機器視覺、數據監控平台之類),預算壓力常常就會莫名膨脹,超出原本預估。大家其實更擔心的,是自己某天會被新系統取代——這種焦慮真的很難消除。
然後就有趣了,多數工廠反饋說,如果改成從小範圍試點切入,比方先對單一生產線進行設備數位化,再慢慢拓展到其他單元,好像風險沒那麼可怕。我前幾天還在想,為什麼大家總要急著一步到位?欸,結果證明分階段反而比較穩。而且由核心種子成員主動參與評估和測試這招,被提起好多次,彷彿他們只要站出來了,就能有效減緩阻力。有些人甚至開始期待轉型過程中的學習機會,不過也有人照舊懷疑啦。總之,看來分階段推動智慧工廠轉型,比一次性全盤更容易拿到內部支持,而且過渡也不至於太劇烈,有時候就是這樣吧。
然後就有趣了,多數工廠反饋說,如果改成從小範圍試點切入,比方先對單一生產線進行設備數位化,再慢慢拓展到其他單元,好像風險沒那麼可怕。我前幾天還在想,為什麼大家總要急著一步到位?欸,結果證明分階段反而比較穩。而且由核心種子成員主動參與評估和測試這招,被提起好多次,彷彿他們只要站出來了,就能有效減緩阻力。有些人甚至開始期待轉型過程中的學習機會,不過也有人照舊懷疑啦。總之,看來分階段推動智慧工廠轉型,比一次性全盤更容易拿到內部支持,而且過渡也不至於太劇烈,有時候就是這樣吧。
模型失效竟是例行檢查漏了?管理迷思全拆解
「AI只要建好就能自動發揮效果」——嗯,這句話啊,現場訪談時大家老是這樣說,好像很理所當然似的。其實仔細想,真不是這麼一回事。每次聽到我都會忍不住翻個白眼,唉,有點懶得吐槽但又忍不住。你知道嗎,有時候喝水都會被嗆,更別說工廠導入人工智慧了,如果忽略模型的持續維護,基本上就是等著出事啦。
因為數據環境或生產條件本來就會變動,不知為何總有人覺得一切穩如泰山。結果預測標準跟決策依據慢慢偏離現況,莫名其妙就走歪了方向。我有遇過機械業者剛開始布建良品檢測系統時信心滿滿,但他們根本沒打算做什麼定期檢核,也沒規劃樣本資料更新,那幾個月下來誤判率整個暴衝,一下子指標亂七八糟。
欸,其實我那天還在想早餐到底該吃什麼,但拉回來講,就算是同樣一套AI,只要團隊有設置例行演算法效能檢查、異常通報和資料調整流程,情況就完全不同。他們可以在問題冒頭時馬上修正AI的判斷基準,大幅減少生產失誤,也比較能保障產品質量不會大起大落。所以啊,「自動發揮」?呵,大概只是希望吧,其實還是得花力氣盯著它跑才行。
因為數據環境或生產條件本來就會變動,不知為何總有人覺得一切穩如泰山。結果預測標準跟決策依據慢慢偏離現況,莫名其妙就走歪了方向。我有遇過機械業者剛開始布建良品檢測系統時信心滿滿,但他們根本沒打算做什麼定期檢核,也沒規劃樣本資料更新,那幾個月下來誤判率整個暴衝,一下子指標亂七八糟。
欸,其實我那天還在想早餐到底該吃什麼,但拉回來講,就算是同樣一套AI,只要團隊有設置例行演算法效能檢查、異常通報和資料調整流程,情況就完全不同。他們可以在問題冒頭時馬上修正AI的判斷基準,大幅減少生產失誤,也比較能保障產品質量不會大起大落。所以啊,「自動發揮」?呵,大概只是希望吧,其實還是得花力氣盯著它跑才行。
Comparison Table:
結論 | 內容 |
---|---|
數據品質至關重要 | 數據雜訊和標註不當會導致AI判斷誤差,影響整體生產效率。企業需重視資料蒐集與校正流程。 |
定期檢查與標註規範 | 必須定期校正感測器並建立清晰的標註規範,以維持資料品質,減少後續錯誤。 |
逐步推進投資決策 | 根據實際狀況逐步推動自動化技術,而非一次性大規模投入,以降低風險。 |
異常監測系統的建立 | 量化異常事件、停機時間及產品成本變動能幫助管理層評估智慧工廠轉型效益。 |
培訓與文化適配 | 關鍵人物的培訓及內部流程優化不可忽視,且每間公司的文化需考量在內以確保方案成功落地。 |
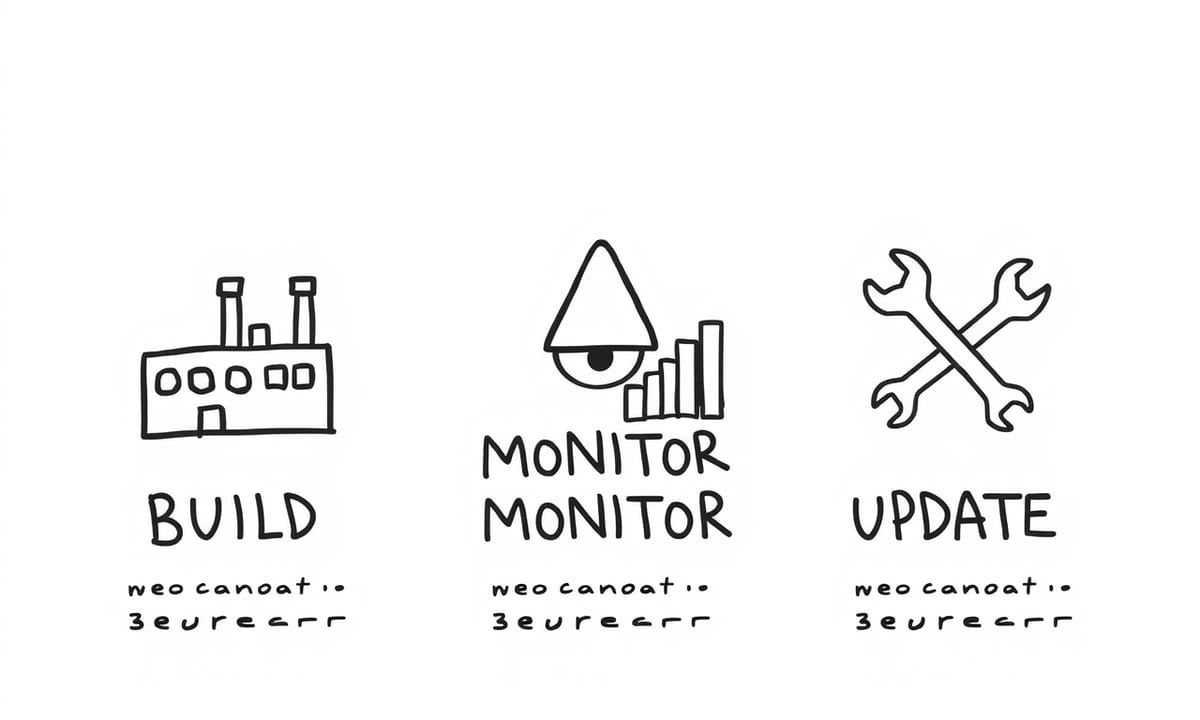
三個月、三條線,小企業轉型到底該先動哪裡?
欸,其實在台灣中小企業輔導現場,大家啟動智慧工廠時,好像都會先摸一摸家底,看自己手上到底有多少資源,再來就是盯著經營上的某些瓶頸。唉,有點無奈,不過也能理解啦。通常他們不是一下子全鋪開,而是小規模、局部試點推著走;畢竟人力跟預算有限嘛,這現實又刺又冷。
講到做法,大部分老闆會鎖定一條線或明確的痛點(比如品質常出包的關卡),嗯……就是沒辦法一次解決所有問題,只能優先攻最痛的地方。話說回來,他們大概會挑三條比較有代表性的產線,然後訂個目標,比如三個月內就要一直抓效率、異常率之類重要數據。
欸,我忽然想到昨天喝咖啡時還有人聊到AI這一塊——不過話題扯遠了,繼續拉回來。在導入AI後啊,他們團隊得自製比對表,那種「導入前VS導入後」的比差幅度,一看就知道改善成效。不只如此喔!還得設計一套簡易即時回報機制,好讓現場每個人都可以馬上記錄新狀況,把訊息捅給研發端,理論上模型才有機會被優化吧,大概吧。
其實,分階段、小範圍驗證好處蠻多,比起什麼事都想一次做完那種大刀闊斧模式,更能掌握風險,也真比較合適中小型組織目前這種活下去為主的運作節奏。我自己偶爾也覺得「一步一步慢慢磨」挺貼近現實,就……很難不嘆口氣,但誰叫資源永遠不夠用呢?
講到做法,大部分老闆會鎖定一條線或明確的痛點(比如品質常出包的關卡),嗯……就是沒辦法一次解決所有問題,只能優先攻最痛的地方。話說回來,他們大概會挑三條比較有代表性的產線,然後訂個目標,比如三個月內就要一直抓效率、異常率之類重要數據。
欸,我忽然想到昨天喝咖啡時還有人聊到AI這一塊——不過話題扯遠了,繼續拉回來。在導入AI後啊,他們團隊得自製比對表,那種「導入前VS導入後」的比差幅度,一看就知道改善成效。不只如此喔!還得設計一套簡易即時回報機制,好讓現場每個人都可以馬上記錄新狀況,把訊息捅給研發端,理論上模型才有機會被優化吧,大概吧。
其實,分階段、小範圍驗證好處蠻多,比起什麼事都想一次做完那種大刀闊斧模式,更能掌握風險,也真比較合適中小型組織目前這種活下去為主的運作節奏。我自己偶爾也覺得「一步一步慢慢磨」挺貼近現實,就……很難不嘆口氣,但誰叫資源永遠不夠用呢?
西方協作東方效率,AI推進路徑能照搬嗎?
「AI不是萬靈丹,得看你怎麼用。」那個自動化設備廠的負責人說這話時臉上一點波瀾都沒有,感覺像在重播某種老掉牙廣告詞。這句話我聽過幾次了吧?嗯,好像不只幾次。其實,在歐美的工廠現場——舉例來說,德國那邊(查資料的時候還看到工業展訪談一直提)——他們老是強調員工要參與、協作彈性很重要,有些地方甚至會拉跨部門小組出來試著把AI混進原本的流程裡。不只是想追求效率,還怕一不小心把團隊氣氛整個壓垮。唉,講到這個我想到之前有人抱怨跨部門開會超煩,不過又回來主題啦。
亞洲企業就明顯不同了欸。台灣、日本尤其明顯,他們偏愛標準化流程——好像什麼都可以複製貼上成功案例。有時候連現場實際需求也乾脆省略,只管產能衝高再說。這種做法其實有點讓人無言,但好像也沒辦法。有專家表示啊,這些差異根本很難用單一模式去說明清楚,所以推動AI前,大多建議組織先盤點自身習慣和溝通方式,大致抓一下哪些步驟適合慢慢導入、哪些應該繞開倫理爭議。不知道為什麼我突然想到上次有公司直接把現場回報機制硬塞給AI模型對接,可惜完全沒考慮使用者操作上的困擾,結果整體效果反而被削弱不少。唉,有時候就是這樣,好像事情總是卡在最意想不到的小節點裡頭。
亞洲企業就明顯不同了欸。台灣、日本尤其明顯,他們偏愛標準化流程——好像什麼都可以複製貼上成功案例。有時候連現場實際需求也乾脆省略,只管產能衝高再說。這種做法其實有點讓人無言,但好像也沒辦法。有專家表示啊,這些差異根本很難用單一模式去說明清楚,所以推動AI前,大多建議組織先盤點自身習慣和溝通方式,大致抓一下哪些步驟適合慢慢導入、哪些應該繞開倫理爭議。不知道為什麼我突然想到上次有公司直接把現場回報機制硬塞給AI模型對接,可惜完全沒考慮使用者操作上的困擾,結果整體效果反而被削弱不少。唉,有時候就是這樣,好像事情總是卡在最意想不到的小節點裡頭。
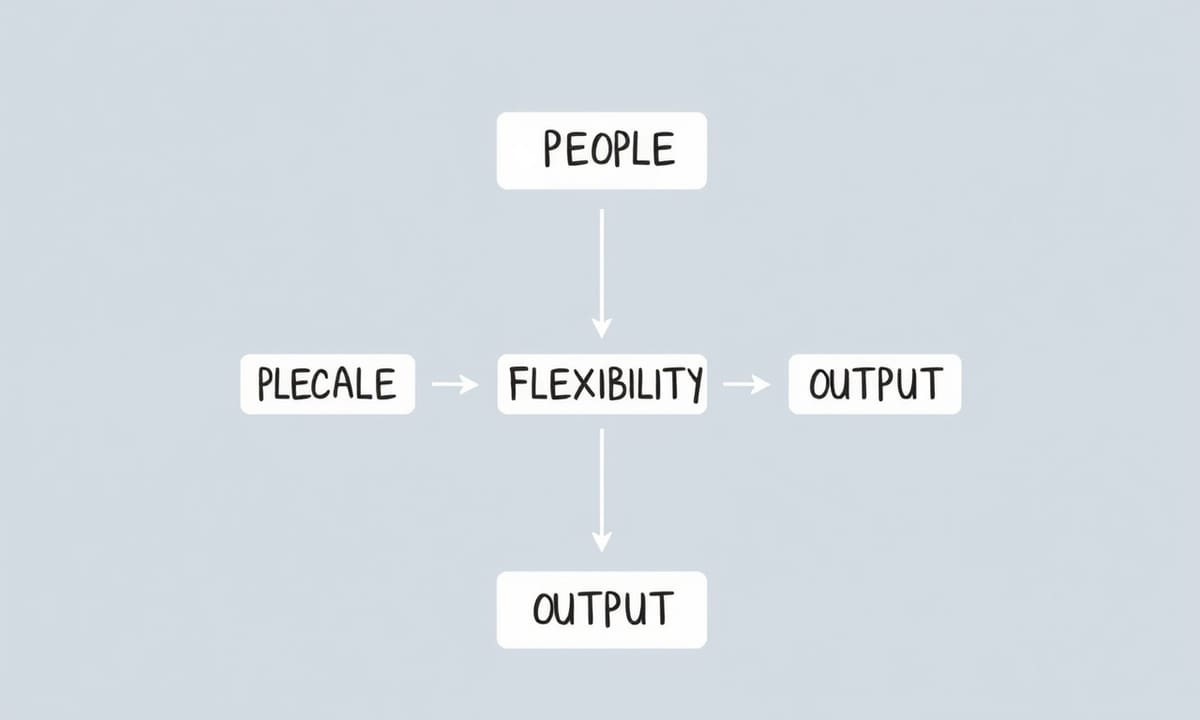
人員同步訓練沒跟上,一步錯全盤皆輸的細節警告
「感測器沒對過,數據分析就跟在沙灘上堆城堡一樣。」欸,其實這話我第一次聽也沒太懂,後來才慢慢體會。現場的技術專員老是念這句,感覺像在碎念,不過…也是有道理啦。AI要部署到產線時,那個流程啊,如果不先從小地方試著弄一遍,再擴大到整條生產線,大概只會更混亂吧。突然想到,上次有人還說什麼「一步登天」,唉,我覺得八成失敗收場。
例如,有家自動化產線,他們最開始是在某條生產線先裝了智能檢測系統,好像花了三個月吧?就是不停地記錄、調整那些細節流程。等差不多摸透之後,他們才敢推廣去別的區域,也因此初期的問題減少蠻多的。有點羨慕那種謹慎的人,畢竟我常常太急躁。
再說啦,現場操作每一步都記下來、定時去複核資料是不是完整,比起光靠模型預測來說,更容易挖出潛在的毛病。不過,有時候寫紀錄真的很煩人,我自己總會偷懶,然後又被罵一頓,但不得不承認這確實比較有效。好吧,雖然偶爾會想放空,但這些小細節真的不能省啊。
例如,有家自動化產線,他們最開始是在某條生產線先裝了智能檢測系統,好像花了三個月吧?就是不停地記錄、調整那些細節流程。等差不多摸透之後,他們才敢推廣去別的區域,也因此初期的問題減少蠻多的。有點羨慕那種謹慎的人,畢竟我常常太急躁。
再說啦,現場操作每一步都記下來、定時去複核資料是不是完整,比起光靠模型預測來說,更容易挖出潛在的毛病。不過,有時候寫紀錄真的很煩人,我自己總會偷懶,然後又被罵一頓,但不得不承認這確實比較有效。好吧,雖然偶爾會想放空,但這些小細節真的不能省啊。
數據有雜訊、人才又斷層,視覺系統憑什麼準確判斷?
說到產業輔導單位,嗯,他們近年調查結果又出來了。其實也不意外啦,每次問這些產線管理者,最棘手的問題總是繞不出去——數據品質老是忽高忽低、技術人員永遠缺貨,再加上系統整合卡卡的,搞得大家都快煩死。唉,有時想想,如果真的哪天能不用煩這三樣該多好。不過回到正題,數據品質這件事特別要命,只要輸入資料裡混著雜訊,或者標註根本亂七八糟,那AI視覺判斷出的誤差就會暴增,可以接近一半之譜。欸,有時候自己都在懷疑,是不是有人存心弄亂?啊,不對,跑遠了。
解決這種麻煩,多數企業當然會把力氣先花在高品質資料蒐集上,比如說感測器剛裝好的時候,就得計劃定期去校正一下、查查有沒有哪裡壞掉之類的異常檢查,同步把標註規範寫清楚點,再拉一套複核機制來補破網。有時候我真羨慕那些標註師居然能一直專注下去。唉,不過想省事直接靠幾個人快速弄完或乾脆跳過驗證流程的人,也不是沒見過,後果咧?後面錯誤只會一層一層疊上去,到最後整條生產線都冒煙。
所以啊,要怎麼辦?資料基礎該打還是得打好,而且SOP不能只是貼在牆上的紙,一定要制定得明確才行。大概只有這樣才能把轉型路上的那些絆腳石減到最低吧。不然誰來收拾爛攤子呢?
解決這種麻煩,多數企業當然會把力氣先花在高品質資料蒐集上,比如說感測器剛裝好的時候,就得計劃定期去校正一下、查查有沒有哪裡壞掉之類的異常檢查,同步把標註規範寫清楚點,再拉一套複核機制來補破網。有時候我真羨慕那些標註師居然能一直專注下去。唉,不過想省事直接靠幾個人快速弄完或乾脆跳過驗證流程的人,也不是沒見過,後果咧?後面錯誤只會一層一層疊上去,到最後整條生產線都冒煙。
所以啊,要怎麼辦?資料基礎該打還是得打好,而且SOP不能只是貼在牆上的紙,一定要制定得明確才行。大概只有這樣才能把轉型路上的那些絆腳石減到最低吧。不然誰來收拾爛攤子呢?
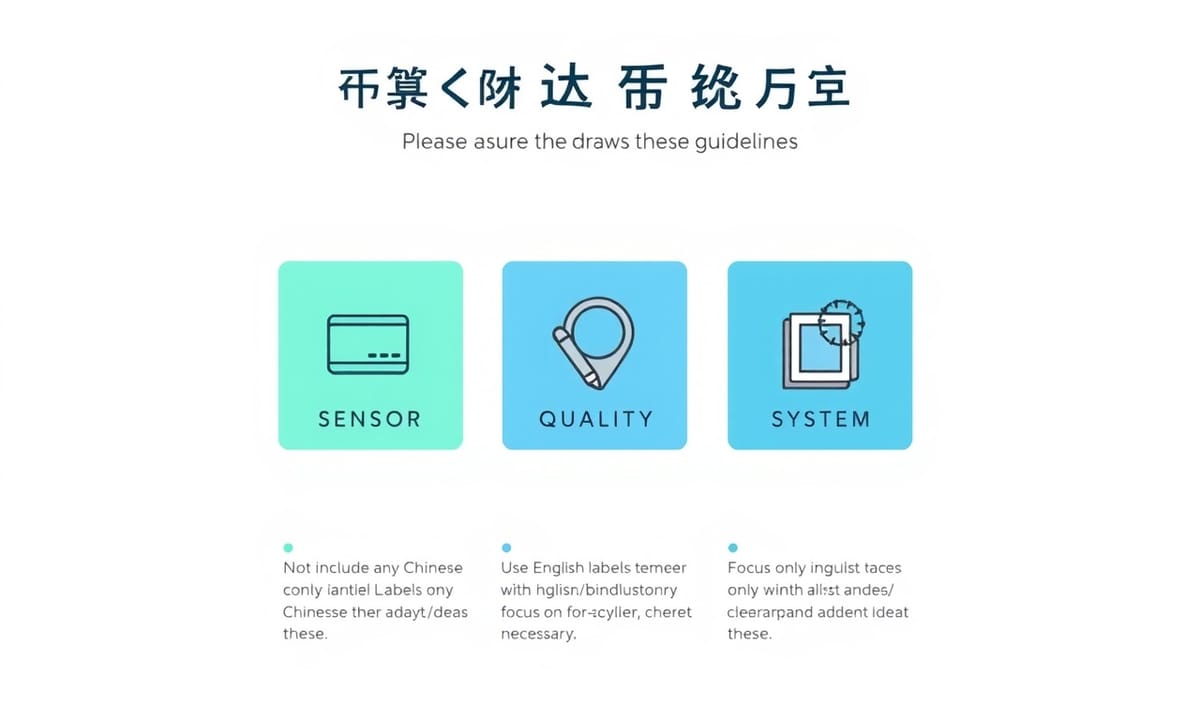
自主機器人風潮來襲,每階段自動化重點你抓到了嗎
最近Rockwell Automation看產業的那種觀察,唉,其實我也不是每一份都能仔細讀完啦,不過他們倒是一直在講智慧製造、然後又自主移動機器人什麼的,推進得滿快的——像是這些自動化系統,現在幾乎已經滲透到各種製造現場。嗯,有時候我會想,那是不是連小型工廠都躲不掉了?但扯遠了。
話說回來,這類方案最有趣的大概就是彈性吧。舉例來說,它們可以讓產線規劃變得更自由,不用每次遇到需求變化就大搬風,而是可以直接調整生產配置。有點像拼圖,但又比拼圖麻煩多了。你看,有些廠區一開始還只是針對某個單一流程先試看看,等真的發現物流效率提上來之後,就會再去把好幾條自動搬運路徑接起來。說起來,好像跟人生決定很像欸——總要先嘗試一下,再決定要不要全力投入。不過我又離題了。
掌握這些技術應用怎麼一步步演變,其實挺重要的啦。因為這樣比較容易判斷自己工廠現在到底適合哪些模組化或擴充式自動化策略,不然亂投資一次砸下去也太可怕。我覺得啦,多半還是需要根據產線的實際狀況,一步一步慢慢推展投資決策,而不是硬要一次做到底,好累。不曉得別人會不會也有相同感觸?
話說回來,這類方案最有趣的大概就是彈性吧。舉例來說,它們可以讓產線規劃變得更自由,不用每次遇到需求變化就大搬風,而是可以直接調整生產配置。有點像拼圖,但又比拼圖麻煩多了。你看,有些廠區一開始還只是針對某個單一流程先試看看,等真的發現物流效率提上來之後,就會再去把好幾條自動搬運路徑接起來。說起來,好像跟人生決定很像欸——總要先嘗試一下,再決定要不要全力投入。不過我又離題了。
掌握這些技術應用怎麼一步步演變,其實挺重要的啦。因為這樣比較容易判斷自己工廠現在到底適合哪些模組化或擴充式自動化策略,不然亂投資一次砸下去也太可怕。我覺得啦,多半還是需要根據產線的實際狀況,一步一步慢慢推展投資決策,而不是硬要一次做到底,好累。不曉得別人會不會也有相同感觸?
設備夠新但流程沒改,這些習慣讓AI白忙一場?
「你真的準備好了嗎?」這句話,唉,每次都被拿來檢查現場狀態,可答案其實往往沒那麼清楚。曾有工廠直接換新機台,還滿興奮的吧?但操作人員還是依賴原本手寫紀錄,結果呢?AI判讀全亂套,真的是一團糟。不過說到底,他們原先就是希望藉由系統減少錯誤,不料卻衍生出一堆例外要處理——數不清那種。
流程裡頭,那些看起來不起眼的小細節,比如輸入動作的延遲、紀錄格式各自為政,其實都會在資料流轉時積成大問題。欸,我好像講偏了……唔,重點是,每次想搞智慧轉型時,你光盤點硬體或軟體根本不夠。有些環節甚至得把每個步驟解構開來,一條一條去檢視潛藏危險,再設計能讓大家反饋與修正的機制。
無論規模多大,大概就都會碰上這種「落差」吧。嗯,有時候還挺無奈的。
流程裡頭,那些看起來不起眼的小細節,比如輸入動作的延遲、紀錄格式各自為政,其實都會在資料流轉時積成大問題。欸,我好像講偏了……唔,重點是,每次想搞智慧轉型時,你光盤點硬體或軟體根本不夠。有些環節甚至得把每個步驟解構開來,一條一條去檢視潛藏危險,再設計能讓大家反饋與修正的機制。
無論規模多大,大概就都會碰上這種「落差」吧。嗯,有時候還挺無奈的。

省成本增產能不是神話,異常率與成長曲線怎樣看才算準?
唉,根據PwC這幾年丟出來的產業報告——有看沒懂的那種——他們說導入AI技術以後,全球製造業在成本控管這塊真的有明顯變化。你可能會想,到底「明顯」到什麼程度?嗯,其實企業現場回饋都很誇張,生產效率一般提升七十多左右,也有人說某些領域能飆到數十倍成長,好像太扯但就是有人這樣講。欸,我剛才還在想中午到底吃了什麼,突然又回到正題。
異常率的監測方面,有將近一半廠商反映現在比以前更快找出問題點,可以縮短修正週期──這聽起來有點厲害,但實際上怎麼計算的我還是會好奇。管理層如果想要把智慧工廠轉型帶來的效益量化,不必太複雜,可以直接盯住自家異常事件發生次數、每季生產線停機時間,再加上單位產品成本變動曲線去追。啊對,我剛剛差點忘記手機還沒充電,拉回主題。
最後,如果搭配資料可視化分析——其實大家最近很愛用圖表炫一下——不只可以讓成果一目瞭然,而且還比較容易看清楚推進過程藏著哪些潛在瓶頸,然後找最佳調整時機,大概就這樣吧。有時候覺得數字跟圖表堆起來人就快眼花,可事情偏偏就得靠它搞清楚。
異常率的監測方面,有將近一半廠商反映現在比以前更快找出問題點,可以縮短修正週期──這聽起來有點厲害,但實際上怎麼計算的我還是會好奇。管理層如果想要把智慧工廠轉型帶來的效益量化,不必太複雜,可以直接盯住自家異常事件發生次數、每季生產線停機時間,再加上單位產品成本變動曲線去追。啊對,我剛剛差點忘記手機還沒充電,拉回主題。
最後,如果搭配資料可視化分析——其實大家最近很愛用圖表炫一下——不只可以讓成果一目瞭然,而且還比較容易看清楚推進過程藏著哪些潛在瓶頸,然後找最佳調整時機,大概就這樣吧。有時候覺得數字跟圖表堆起來人就快眼花,可事情偏偏就得靠它搞清楚。
本段資料來源:
- 2025 AI Business Predictions - PwC
Pub.: 2024-12-03 | Upd.: 2025-06-16 - PwC`s Global Artificial Intelligence Study: Sizing the prize
- PwC`s AI Agent Survey
- AI Technologies: Overhyped, imperative or real opportunity?
- The game-changer – roles and impact of AI - PwC Belgium
Pub.: 2025-01-09 | Upd.: 2025-01-15
人機協作之外:商業模式與永續責任的新想像
工業5.0嘛,其實聽起來就有點未來感,主打的是人機合作還有什麼商業模式創新。不過,唉,我最近腦袋總是卡住——Rockwell Automation不是前陣子才提到,自主移動機器人正在慢慢把產線彈性往上推嗎?這到底是真的會大改變還是只是行銷話術呢?嗯,不管怎樣,說回正題好了。現場在真的要做的時候,他們建議其實可以先針對那種一眼看得出問題的痛點下手,就設個小型AI試辦區域,然後邊做邊把流程細節記錄清楚。欸,但資料品質又是一回事喔——常常資料雜訊一堆,所以最好定期檢查、標註一下,不然模型判斷容易被干擾。
想到組織內部層面,有些人覺得只要買器材就好,其實不然啦。關鍵人物培訓很重要(這句我自己也講膩了),而且流程優化不能停滯,再加上異常通報和反饋系統要一起建立。我剛突然想到早餐吃啥…啊差題了,拉回來。如果預算有限也是大家普遍的困境,只能從單一流程慢慢開始導,一步步擴張範圍,這樣比較少阻力,也比較好看到是不是真的有效果。
部署新技術時千萬別忘本喔,每間公司文化不同,你硬照搬外面的模板,有時根本水土不服。至於發展目標和永續責任什麼的,也最好提前納入評估指標裡,不然最後可能整套方案都沒方向,大概就像摸黑找路吧。(唉,好像又碎念太多。)
想到組織內部層面,有些人覺得只要買器材就好,其實不然啦。關鍵人物培訓很重要(這句我自己也講膩了),而且流程優化不能停滯,再加上異常通報和反饋系統要一起建立。我剛突然想到早餐吃啥…啊差題了,拉回來。如果預算有限也是大家普遍的困境,只能從單一流程慢慢開始導,一步步擴張範圍,這樣比較少阻力,也比較好看到是不是真的有效果。
部署新技術時千萬別忘本喔,每間公司文化不同,你硬照搬外面的模板,有時根本水土不服。至於發展目標和永續責任什麼的,也最好提前納入評估指標裡,不然最後可能整套方案都沒方向,大概就像摸黑找路吧。(唉,好像又碎念太多。)