幫助工程師於高精度光傳送模組自動化製程中快速穩定提升良率並減少夜間加班。
- 檢查每一批次自動對位設備校正誤差,確保≤0.1μm才啟用量產。
提前發現偏移能大幅降低後續品管瑕疵率,免除重工困擾。
- 將關鍵流程環境溫度波動控制於±1°C內,自動記錄每小時一次。
溫控穩定,能有效壓低熱膨脹導致的Z軸微誤差,維持精密對位品質。
- 列出所有材料熱膨脹係數,選用差異不超過10%的搭配組合優先實驗。
材料屬性一致,有助製程長時間保持納米級定位精度。
- *導入AI視覺公差補償系統,每週分析一次歷史修正紀錄*
*即時偵測異常趨勢,有效預防突發性人為失誤影響產線連續運作*
從手動到自動化,光通訊產業的轉型之旅
說到光通訊產業的自動化,Lio這個名字幾乎總是在現場討論裡出現。其實剛開始時,大家還是習慣用手去調那些細微的位置,有點像在玩一種考驗耐心的遊戲。Volt那邊好像也是這樣,一直到某一天,自動對位突然變得沒那麼遙不可及。系統會自己修正小偏差,那速度說不上秒殺,但的確快了不少。有些人本來還半信半疑,後來卻被結果嚇了一跳。轉折發生時,好像也沒什麼隆重儀式,只是一切慢慢不一樣了。
掌握關鍵細節,避免光傳送模組生產中的失誤
那些年,我們在光傳送模組生產線上踩過不少坑,像是石英載具的清潔週期若管控不當,很容易導致報廢量直線上升。更要命的是,許多團隊忽視了溫控與換氣頻率的微妙平衡,這些看似瑣碎的細節,卻可能在不經意間造成難以挽回的生產損失。每一個失誤背後,都是血淚交織的技術成長,也是產業鏈中不可或缺的寶貴經驗。
Comparison Table:
結論 | 影響因素 | 應對措施 | 關鍵技術 | 未來方向 |
---|---|---|---|---|
材料特性變化影響產品品質 | 溫度、濕度等環境條件的變化可能導致零件形狀與尺寸不穩定 | 引入自動補正機制以降低人為差錯及提高良率 | AI視覺補償系統,能根據不同特徵自動調整方法 | 持續優化AI演算法與數據分析能力 |
生產過程中的微小瑕疵可能造成重大影響 | 假性對準和細節忽略導致的失誤累積問題 | 加強工程師對於聲音和觸感的敏感度訓練,以辨識真實對準狀態 | 經驗法則與AI系統相輔相成,提升整體生產效率 | 開發多層次公差管理架構,進一步減少風險 |
自動化系統初期需密切監控各項數據變化 | 前期良率低迷,需找出問題源頭並逐步修正流程 | 依賴歷史數據及即時反饋進行調整 | 重視報表分析,尋找改進契機 | 建立更完善的資料庫以供後續參考 |
精密對位是一場綜合性的挑戰 | 多種因素交織影響最終結果,包括工藝、環境、人為操作等 | 採用分階段公差管理策略,以便針對不同問題做出有效修正 | 透過模擬測試預測潛在問題並提前介入 | 提升團隊協作與知識分享文化。 |
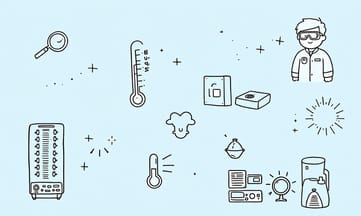
工藝流程與環境變數如何影響精密對位?
有時候現場氣氛就像壓著一層細微的緊張,尤其是在那些光學對位快要進入關鍵階段時。大家圍在機台旁邊,偶爾有人低聲討論,好像怕打擾了什麼看不見的秩序。燈光反射在桌上工具與載具表面,有些地方乾淨得發亮,也有幾個角落總是怎麼擦都還會留點指紋。空調聲音混雜著鞋底摩擦地板,每一次校正步驟拖長了時間,就有人開始懷疑是不是哪裡參數又跑掉了。有些老工程師說這種感覺像是下雨前悶熱的天氣,什麼事隱隱約約要發生卻還沒來。專有名詞聽多了也容易混淆,比如那個自動調整程式和之前手動設置到底差多少,有人說其實相差將近一半,也有人覺得只是心理作用。不過只要顯微鏡下那條線再對準一點,整間廠房好像才真正鬆口氣。
三大黑科技如何突破自動對位的瓶頸?
在光傳送模組的生產線上,Lio曾遇到許多令人頭疼的技術難題。其中,石英載具的清潔管理一直是一個容易被忽視的關鍵環節。不當的清潔週期會導致載具表面殘留微小雜質,進而引發報廢量激增的連鎖反應。另一個常被輕忽的細節是溫控與換氣頻率的精準搭配。不同的生產批次若未能妥善調控環境參數,輕則影響產品一致性,重則造成整批次產品品質下滑。這些看似瑣碎卻極其關鍵的生產細節,曾讓不少技術團隊付出慘痛的學習代價,也凸顯了精密製程中每一個環節的重要性。
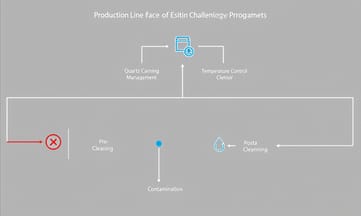
0.1μm的突破瞬間,Z軸誤差巧妙轉換成XY修正
「誤差七十多奈米?你沒算錯吧?」有人這樣問,Lio聽了只是笑,說現場調整的時候其實比想像還難抓。有時候剛換完載具,清潔流程忘了一步,結果報廢量就莫名多起來。旁邊工程師又補一句:「溫度有變動過嗎?我記得前幾次就是因為那個冷氣開太久。」他們開始翻舊紀錄,也不是每次都能對上。另一頭,有人提到換氣頻率,好像也和某次設備異常有點關係。這些細節每次討論都會冒出新版本,沒人敢說自己全對,只知道一旦出錯,就是一整批要重來。
熱膨脹係數挑戰下,我們能怎麼應對材料特性?
在光傳送模組的製程中,材料本身的物理特性彷彿是一場永無止境的對決。每一種材料都有其天生的脾氣,溫度的微小變化就像是一場看不見的戰爭,悄然改變著零件的形狀與尺寸。工程師們彷彿在與這些無形的敵人對抗,卻總是稍慢一步。即便採用再精密的控管手段,材料內部的分子運動依然我行我素,不受控制。這種看似微不足道的變化,卻可能在精密對位的世界中造成難以想像的連鎖反應,讓原本精心設計的製程瞬間失去平衡。
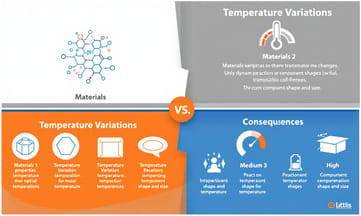
自動化引入後,人為失誤如何驟降至低點?
剛開始自動化系統導入那幾天,現場工程師之間討論聲音沒停過。光是前一週,不同工段的良率還卡在七十多,大家也說不清到底是哪個環節出狀況。直到調校流程進行到第二週中段,有人發現光學座標偏移好像突然變少了,一些原本常見的小瑕疵也慢慢消失。有人說是參數終於穩定下來,也有人懷疑是不是運氣好,但實際上那段期間產線報表上的良率數字變化很明顯——差不多兩週後就飆到將近全線都過關。這種劇烈躍升,廠內老員工都說沒碰過類似的經驗。不過仔細想想,真正影響最大的或許還是在於自動補正機制介入,讓之前那些微小的人為差錯一下子被壓到極低,到底是巧合還是必然,其實也說不上來。
老廠長的現場智慧,簡單技巧帶來意想不到的效率提升
在光傳送模組產線的日子裡,老廠長曾不只一次教導我辨識「假性對準」的微妙技巧。他總說,有時看似完美的對準,其實暗藏玄機。我記得他示範過,輕輕按壓治具時,會用耳朵聽那微妙的聲響變化,好像在解讀機器的秘密語言。有次他抓住我的手,讓我感受那不經意間的細微震動,說這些都是機器想要隱藏的小細節。他強調,真正的對準不只是目測,更要用聲音、觸感去感知,那些經驗是無法用儀器完全取代的工藝智慧。
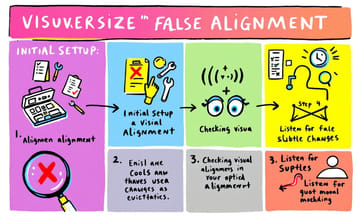
AI視覺補償在公差管理中的多層次應用究竟是什麼?
聽過某些工程師討論AI視覺補償的時候,總覺得這套系統好像有很多層,不是單一對準那麼簡單。有人提到,公差管理要分階段來做,有時候直接修正零件表面的小偏差,但也有狀況是需要先判斷組裝環節裡哪個步驟出錯,好像多一道保險。不過,現場其實沒幾個人能說清楚到底怎麼劃分每一層,只知道AI會根據不同特徵自動選擇調整方法。偶爾有誤判,也不是什麼大事,畢竟整體風險下降了不少。這種多重補償邏輯,大概是最近幾年才慢慢成熟起來的吧,早期還常靠經驗法則補洞。
閉迴路控制機制如何確保精密製程的一致性品質?
就像山路上的登山客需要不斷調整腳步,光學對位也是一場精密的步伐校正。生產線上的工程師們,彷彿在一條佈滿細微岔路的山徑中前進,稍有不慎就可能偏離正確軌道。我們聽說過許多慘痛的經驗:有如石英載具清潔週期失控,造成大量零件報廢;又如忽視了溫控與換氣頻率的微妙平衡,讓整條生產線付出慘痛代價。這些看似瑣碎的細節,就像山路上被忽視的小石子,卻可能讓整個旅程功虧一簣。