你可以這樣做 - 協助企業智慧製造轉型,快速提升效率與競爭力
- 優先導入AI或IoT方案於單一產線,三個月內明確追蹤生產效率變化。
有助降低初期投資風險,同時用數據驗證成效再逐步擴大。
- 每半年檢查並精簡紙本作業比例,力求減少10%人工作業。
持續推動數位化可減少錯誤、加速資訊流通,讓現場管理更即時透明。
- 定期盤點跨部門合作項目,每年最少新增兩項流程共創改善計畫。
橫向協作提升知識流通,有效突破組織轉型阻力。
- 建立新技術教育訓練SOP,新員工7天內需完成操作演練並回饋困難點。
*即時支持*能消除員工疑慮,確保自動化導入順利不拖慢產能。
智慧製造如何成為全球產業升級的核心推動力?
「在歐洲幾年前的產業論壇上,現場專家提到:『現在工廠裡頭,機器和資料互通變得稀鬆平常。』這種情形其實不僅限於大型企業,小規模廠房最近也開始嘗試導入自動化工具。說穿了,智慧製造或者說數位工廠,不再只是高科技公司的專利,連傳統產業也陸續跟進。像有些加工部門會從比較簡單的監控系統開始下手,再慢慢擴大到遠端協作或流程優化。不過,有人以為只要添購新設備就能達標,但現場經驗顯示,更重要的是日常數據如何被收集、讀懂,還有怎麼配合原本的人工作業重新調整。當然,中間碰壁的例子也不少,例如太快更換軟硬體反而干擾生產,大概七成左右的使用者後來選擇循序漸進。這種做法雖然看似緩慢,但往往更容易在現實條件下穩定運作。一邊摸索一邊調整,其實挺符合現在這個轉型時代的步調。
傳統企業在數位轉型中面臨哪些困難與挑戰?
「老一輩師傅都還是用手抄表,換成掃描條碼,不知怎麼下手。」這種聲音,現場聽過不只一次。其實除了人員習慣難改,像設備彼此不能講話、資訊散落在不同紙本或系統裡,好像處處都是卡關點。有人會想:要不要直接全部換新?但預算有限,又怕砸下去效果有限。假設工廠規模在七十多人的時候,一個流程改動牽動的部門比想像中多;那如果老舊機台又沒有數據介面,要接進系統,到底該先做哪一步?有的人說買標準化方案省事,但遇到例外狀況時,反而容易跑不動。這些困境,是不是跟產業特性有關,還是只是資源分配的問題?現場經驗有提過,有些管理層會遲疑:「花了錢真的值嗎?」結果導入後卻發現流程斷裂或資料不同步。另一邊,有廠商強調技術升級能帶來效率,但細算成本、停工時間、培訓週期,加起來也沒那麼明朗。看起來,傳統模式下的企業,每跨一步都得衡量好多因素,不只是技術夠不夠,也包括人和組織能不能跟得上——這些問題,好像永遠沒有標準答案。
Comparison Table:
結論標題 | 智慧製造轉型的關鍵要素 | 企業成功案例分析 | 常見挑戰與解決方案 | 最佳實踐建議 |
---|---|---|---|---|
員工情緒管理 | 透過私下對話釋放焦慮,增進員工信任感。 | 中型企業因靈活性行動迅速,情緒穩定較快。 | 初期不安與抗拒需透過有效溝通管理。 | 設置匿名意見箱提供反饋管道,建立開放心態。 |
技術導入策略 | 先盤點現有流程與痛點,再設定分階段目標。 | 成功案例多半涉及外部顧問介入協助調整。 | 避免單一資訊系統無法整合老舊資料的困境。 | 採用多方評比工具確保選型合理,降低風險。 |
部門協作方式 | 透明會議間促進即時交流,提高問題解決效率。 | 不同部門人員共同討論減少推託情況發生機率。 | 新流程初期可能出現摩擦,但補足訊息可減少誤解。 | 輪流坐鎮提升跨部門合作意識和凝聚力。 |
培訓效果提升方法 | 分批次短周期實戰演練提高學習成效近50%。 | 大規模一次性講座效果有限,需改進為小組互動式教學方式. | ||
專案管理控制策略 | 使用簡易專案管理模板追蹤進度與資源配置. | 遇到卡關時回顧目標與資源,不盲目推進. | 量化指標設立以便於檢視成果與調整方向. |
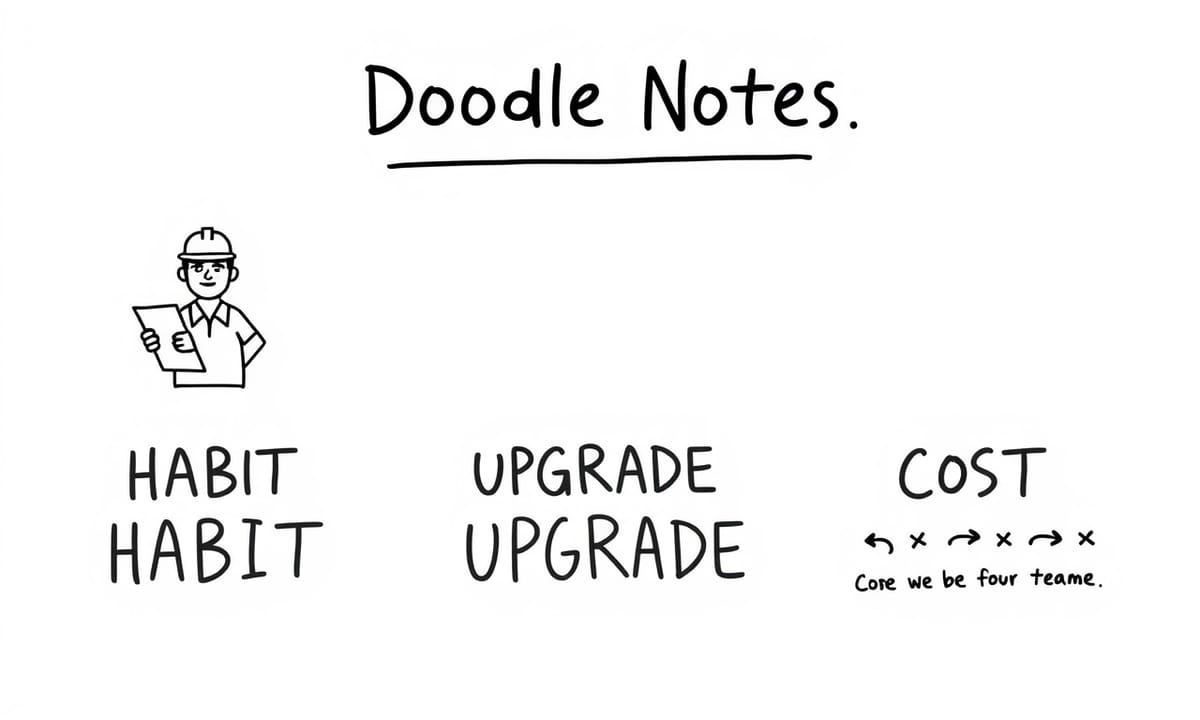
為何中小企業的數位轉型速度遲緩,該如何突破?
「中小企業多半還在摸索自動化,這句話產業界聽了不陌生。工研院大約三年前有份調查提到,製造業裡能真正跳到數位整合階段的企業數量並不多,尤其規模較小的單位容易卡關。其實汽車、電子等資本密集產業起步早,反而傳統行業像金屬加工或食品相關,好像七十多家只有個位數進展到智慧製造。這些年各種推動方案陸續出現,有人強調導入MES系統先理流程,也有人主打感測器布建直接蒐集資料,不過兩者路線都遇過:一沒盤點清楚現場狀況就照搬方案,結果投資回收期拉長;另一邊則是什麼都想做卻沒聚焦。細看下來,不同產業、規模和設備老舊程度,決定了方法選擇;其實沒有哪種做法永遠適用,大致只能說根據自家成熟度分階段嘗試,比較能避開踩雷。
從小規模試點出發,降低風險的最佳策略是什麼?
「前陣子在中部某間老牌工廠,經理提到:『我們不是一開始就大範圍導入,而是先挑一條線做測試。』這種分階段嘗試的作法,似乎成了不少業界的默契。通常會先從標準化程度高、容易量化效益的小環節下手,例如包裝自動化或檢測流程改造——畢竟這些地方如果出狀況,也比較不會牽連全局。人力配置和預算規模有限時,把資源集中用在這些明顯可見、好追蹤成果的地方,有助於減少風險。後續若初步成效還行,再慢慢延伸到其他區域。反而有人急著一次全面上馬,結果卡在數據混亂、人員反彈,最後不得不暫緩。所以小規模試點,不只是技術問題,更像是在調整組織節奏。
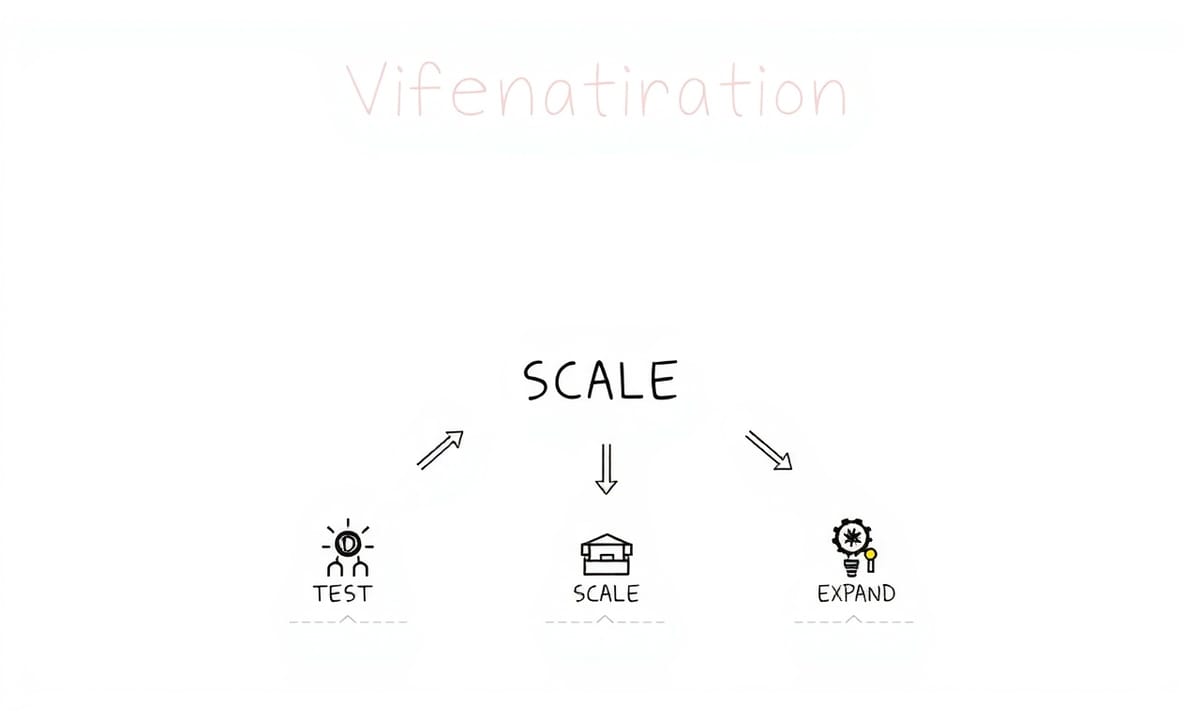
整合多種技術能否提升智慧工廠的生產彈性與效率?
「每一套智慧工廠的系統,看起來都像在拼圖桌上慢慢組合。AI模組、感測器資料串流、自動化手臂軟體等零件,各自有點不太一樣的形狀,彼此之間要貼合得剛好,不是說規格對上就沒問題。有些現場工程人員會發現,雖然控制台標榜通用接口,但不同品牌之間的數據傳遞偶爾還是卡住——這種時候,彷彿有人拿錯了一片拼圖。若忽略技術協同,初期運作或許看似順利,可等到擴充新產線或增加設備後,那些未理清的小縫隙才會浮現。據電子製造場域這幾年來的經驗,只要缺乏標準化設計,將近一半案例最後都需額外投入時間與成本調整對接方式。其實,把關鍵技術搭配當成拼圖,每步留白一點空間做預留,比事後拆解重拼更省力。
員工對自動化變革的疑慮,該如何有效解決?
「剛開始推動智慧製造時,現場一名資深員工低聲說,‘這些機器真的會取代我們嗎?’那一刻氣氛有點凝重。有人表面上沒多話,其實私下經常討論要不要轉職,或者乾脆先學點別的技能備用。後來管理階層也注意到這種情緒,不再只是開會宣導,而是找幾個比較有影響力的同仁私下聊聊,慢慢釋放焦慮。有次小組會議中,一位工程師主動分享自己試著參與新設備維護流程的過程,雖然有些步驟摸索很久,但最後還是找到訣竅,也讓其他人看見不是一下子就被淘汰。現場主管後來建議,每逢引進新技術,都安排簡單的現場操作演練,不用太正式,大家可以輪流嘗試操作、提出問題,有疑慮當場討論完。這種方式比起傳統只發文件或開教育訓練課程,好像更容易讓人願意敞開心胸。另外有段時間,公司內部設了匿名意見箱,只要有人對變革不放心,就能直接反映給決策層,這招雖然效果有限,但至少提供了一個出口。不知是不是因為這樣,大概過了一季左右,多數人的情緒才漸漸平穩,不那麼排斥新流程。
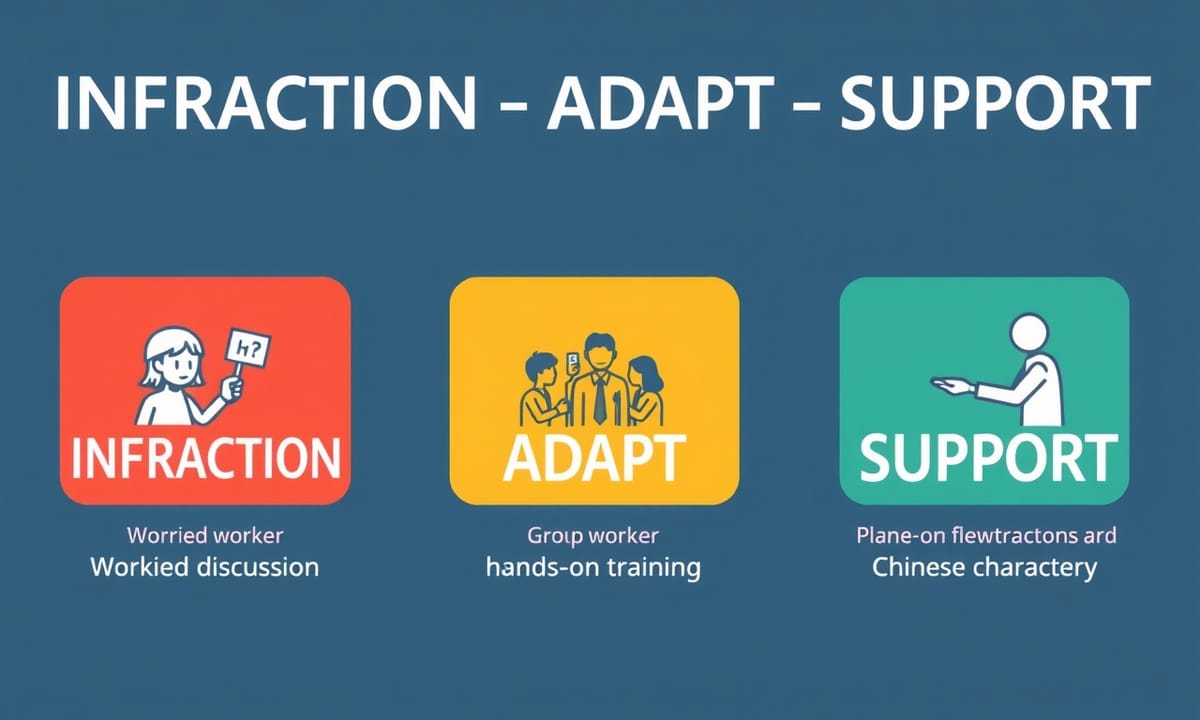
全球智慧工廠市場未來潛力有多大,投資意義何在?
根據產業觀察,智慧工廠相關投資近幾年明顯有增無減。舉例來說,歐洲地區在疫情後的製造產業重整期間,智慧生產線導入率大約是三成出頭(Statista 2023),遠高於過往傳統自動化階段。有趣的是,有些中型企業反倒比大型集團行動更快,原因可能跟靈活調整結構、決策流程短有關。而效益層面,大約七成廠商表示人力成本下降、能源利用效率提升最為明顯;少部分則提到庫存周轉速度增加。不過,也不是所有案例都一帆風順,有遇到資料串接斷點、初期技術磨合等問題。有時候這些數字背後,其實還藏著不同產業特性與區域政策推動節奏。
本段資料來源:
中國製造業成熟度現狀與常見誤區,你了解多少?
「企業最常問:是不是買了自動化設備就算轉型?」一位顧問搖頭:「這種想法在不少廠區聽過,結果流程沒理順,反倒多出新問題。」另一個現場負責人提到,他們一開始只換上單一資訊系統,本以為能提高效率,但後來發現很多老舊資料無法整合,還得請外部專家協助。有人追問:「那應該怎麼分階段?」專家解釋,大致可以先盤點現有流程和痛點,再規劃短中長期的目標,每階段都設可量化指標,比起一次砸大錢來得穩妥。其實將近一半的企業,在落實時還是容易陷入『技術萬能』的迷思,真正有效果的案例,多半都有外部顧問介入評估與持續調整。
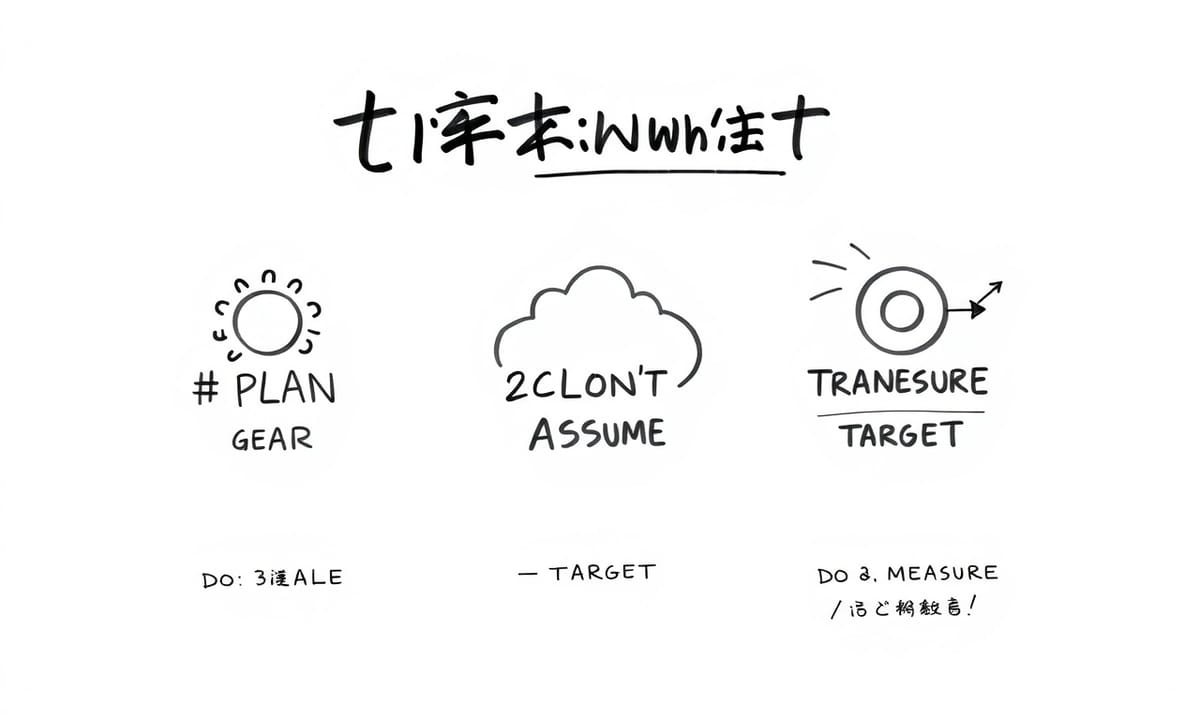
跨部門協作文化如何幫助減少組織阻力並促進知識流通?
「你們看,這條產線上,不同部門的人幾乎隨時聚在一起討論。」一名現場主管邊走邊指著窗後的透明會議間。玻璃牆貼滿便條紙,上頭寫著各種機台狀況、維修進度甚至是早班交接的小細節。比起只靠一份報表,這樣的同步溝通讓問題好像比較不容易卡關。常見情況下,技術人員和品保或物流其實分屬不同單位,但在這裡,他們輪流坐鎮,每天至少有七十多個小型協作碰面。先前據日本工廠(2022年)觀察,有提到類似做法能降低部門之間來回推託的情形。不過也不是每一次都很順利,有時新流程剛開始會遇到些摩擦,比如資料格式不統一或者臨時缺席導致溝通斷層。有人說,只要訊息交換能及時補足,長遠下來反而減少了誤解與重工的機會——現場氛圍因此慢慢變得比較緩和。
完整的解決方案流程包含哪些關鍵要素與管理技巧?
「初期聚焦於單一關鍵業務流程,反而讓資源有限的團隊更快看見成果。」這句話在產業升級案例裡反覆被提到。有些企業急著想全盤導入新系統,結果常陷入冗長調整與需求不明確的迴圈。其實,可以先列出目前最迫切需要優化的流程,比如有公司選擇以供應鏈資訊自動化作為起點,再逐步拓展。選型時,建議採用多方評比工具(如TCO模型),釐清直接與間接成本。系統導入階段,不妨善用外部顧問協助梳理細節,但也要同步指派內部專責窗口負責溝通協調。員工培訓方面,比起大規模一次性講座,有團隊改為分批次、短周期實戰演練,效果據說提升了將近一半。控制進度時,用簡易專案管理模板即可追蹤重點環節,遇到卡關隨時回頭檢視目標與資源配置,而非一味推進不回頭。