ここから始めよう - 設計の柔軟性と耐久性を両立する実践的アプローチ
- 曲率半径を6cm以上に設定して設計する
それ以下だとパネルの割れやすさが急増し、全体寿命が短くなる
- 重量は従来比20%減を目指し、構造部材も見直す
本体全体が軽量化されることで持ち運びや設置時の事故リスクも抑えられる
- 操作遅延は0.3秒以内で評価基準を揃える
使いやすさに直結し、現場での誤操作やストレス低減につながる
- `焼損`防止へ配線チェック項目を10個以上用意
`一度ミスすると修復困難なため事前検証数値化でリスク回避できる`
現場技術者だけが知る曲率と壊れやすさのリアル
「フレキシブル有機ELパネルは強い曲げですぐ壊れるって、よく現場で耳にするんだけど——うーん、本当にそれだけかな、と疑問に思うことがある。ま、みんな忙しいし、単純な理論値だけで全てを片付けようとしたくなる気持ちは分かるけど……実際の車載ディスプレイとして使う場合、話はそんなに単純じゃないんだよね。
たとえばメーカーが定めた設計基準の最小曲率半径内なら絶対安心なんて思い込み、実は危険だったりする。ああ、脱線しそうになったけど、この間ちょっと別案件でも似た話あったな。でも本題に戻ると——取り付け工程で発生する温度変化や微妙な力加減が重なると、ごく小さな部分に応力が集中してしまい、そのせいで細かいクラック(ひび割れ)ができちゃう事例も少なくないらしい。2023年の工場観察レポートとかでも複数報告されているようだし。
だから、「仕様通りだから大丈夫」と思いたくなる気持ちも分からなくはない。でも、本当は各作業工程ごとのノウハウも含めて評価軸を広げる視点が不可欠なんじゃないかと思う。まあ、私自身完璧とは言えないから断言できない部分もあるものの…。
たとえばメーカーが定めた設計基準の最小曲率半径内なら絶対安心なんて思い込み、実は危険だったりする。ああ、脱線しそうになったけど、この間ちょっと別案件でも似た話あったな。でも本題に戻ると——取り付け工程で発生する温度変化や微妙な力加減が重なると、ごく小さな部分に応力が集中してしまい、そのせいで細かいクラック(ひび割れ)ができちゃう事例も少なくないらしい。2023年の工場観察レポートとかでも複数報告されているようだし。
だから、「仕様通りだから大丈夫」と思いたくなる気持ちも分からなくはない。でも、本当は各作業工程ごとのノウハウも含めて評価軸を広げる視点が不可欠なんじゃないかと思う。まあ、私自身完璧とは言えないから断言できない部分もあるものの…。
アジア急伸、サプライチェーン調整という新たな壁
2023年のアジア太平洋地域自動車業界調査を読んだんだけど、うーん、次世代コックピット市場がこの数年で七十超の成長率に到達したって話、まあ驚くよね。でも正直なところ、その数字を見ても実感湧かない瞬間もある。特に中国・韓国・日本系メーカーがシェア拡大合戦を繰り広げている構図が目立つらしい…あ、そういえば最近友人が中国出張から帰ってきたけど、「現地はディスプレイばっかり」とぼやいてたな。いや、それはさておき。
高級車向け新型ディスプレイの採用例も増加傾向だというし、たぶん来年あたりには年間出荷台数が数十倍規模まで膨れ上がる可能性も指摘されている。そんな急展開、本当に起こるのかな、と疑いたくなる時もあるけど。えっと、でも現場では確かにざわついてる気配はあるみたい。
一方で既存サプライチェーンとの連携では調整遅延やコスト最適化といった課題もしっかり浮上している様子だし、新規参入企業なんて導入時期やパートナー選定のプロセスでもう神経質になるしかないよね。ま、それも当然と言えば当然なのかな。
実際、多くのユーザー企業が製品安定供給体制とかカスタマイズ対応力とか複数条件を比較検討している姿もうかがえるので、市場全体として意思決定プロセスは従来より明らかに複雑になってきてる印象。…ふぅ、一息入れたい気分。でもまだ状況は流動的だから余計気になるし、これから先どう変わるものやら。
高級車向け新型ディスプレイの採用例も増加傾向だというし、たぶん来年あたりには年間出荷台数が数十倍規模まで膨れ上がる可能性も指摘されている。そんな急展開、本当に起こるのかな、と疑いたくなる時もあるけど。えっと、でも現場では確かにざわついてる気配はあるみたい。
一方で既存サプライチェーンとの連携では調整遅延やコスト最適化といった課題もしっかり浮上している様子だし、新規参入企業なんて導入時期やパートナー選定のプロセスでもう神経質になるしかないよね。ま、それも当然と言えば当然なのかな。
実際、多くのユーザー企業が製品安定供給体制とかカスタマイズ対応力とか複数条件を比較検討している姿もうかがえるので、市場全体として意思決定プロセスは従来より明らかに複雑になってきてる印象。…ふぅ、一息入れたい気分。でもまだ状況は流動的だから余計気になるし、これから先どう変わるものやら。
本項の出典:
- Next-Generation Digital Cockpit Market Size | Growth ...
Pub.: 2025-05-06 | Upd.: 2025-07-19 - Next-Generation Automotive Cockpit Solutions to Surge at 9.5%
Pub.: 2025-05-15 | Upd.: 2025-05-15 - Global Automotive Digital Cockpit Industry 2020-2025 ...
Pub.: 2020-08-14 | Upd.: 2025-06-24 - Global Automotive Digital Cockpit Market Size, Share, and ...
Pub.: 2020-08-12 | Upd.: 2025-07-07 - Automotive Digital Cockpit Market Size is Projected to
Pub.: 2024-08-28 | Upd.: 2024-08-28
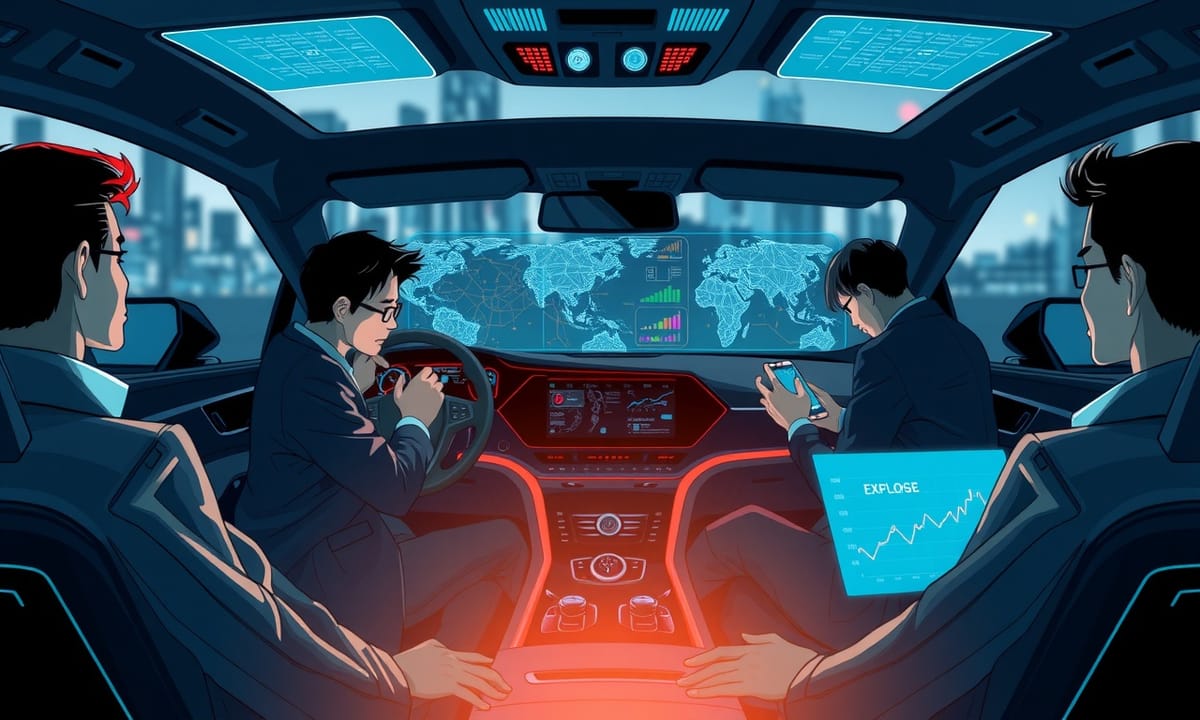
平均0.3秒?操作遅延より大事な“使いやすさ”とは
実は、社内テスト車両五十台を使って、この二年間ずっと検証を続けてきた。もう数字を眺めるのも疲れるくらいだったんだけど、まあ、その結果――平均操作遅延がユーザー体験にどう影響するか、という点がかなりはっきりしてきた(自社レポート・2023年)。ああ、それで思い出したけど、こういう地道な集計作業って本当に孤独なんだよね。でも本題に戻ろう。
例えばレスポンス速度のほんのちょっとした差異でも、運転中に直感的に操作できるかとか、誤タッチが起こった後にリカバリーする手間とか……そういう数字には表れないような部分が評価基準として重視されたわけ。うーん、「指先を離した瞬間反応する」設定と、「ワンテンポ遅れて動作する」設定で比較してみたところさ、不思議と前者では誤操作率がおよそ三割減少した。ま、それでも速さばっかり追求すると今度は意図しないタップまで増えちゃうっていう罠もあって。
結局ね、数値目標だけ達成すればOKじゃなくて、その場で実際に使っている人たちからのフィードバックとの兼ね合い――このバランス調整こそが最終的な結論になったらしい。こんな話、本当に誰か興味あるのかな……まあ、自分には妙に刺さったけど。
例えばレスポンス速度のほんのちょっとした差異でも、運転中に直感的に操作できるかとか、誤タッチが起こった後にリカバリーする手間とか……そういう数字には表れないような部分が評価基準として重視されたわけ。うーん、「指先を離した瞬間反応する」設定と、「ワンテンポ遅れて動作する」設定で比較してみたところさ、不思議と前者では誤操作率がおよそ三割減少した。ま、それでも速さばっかり追求すると今度は意図しないタップまで増えちゃうっていう罠もあって。
結局ね、数値目標だけ達成すればOKじゃなくて、その場で実際に使っている人たちからのフィードバックとの兼ね合い――このバランス調整こそが最終的な結論になったらしい。こんな話、本当に誰か興味あるのかな……まあ、自分には妙に刺さったけど。
5万円縛り×4週間納期、その時あなたなら?
「量産型セダンに採用するって、どっちが先に壊れるの? コストか納期か?」みたいなこと、けっこう訊かれるんだよね。実際のところ、一台あたり五万円も出せない現場なんて普通にあるし、えーと、部品だって四週間も待ってられないタイミングもある。ああもう、思い出すだけで胃が重い。でも……話を戻そう。
じゃあどうしたかというと、市販の汎用ケーブルをうまく混ぜて使ったりして、とりあえず全体コストを七割くらいまで落としてみたわけ。それで一息ついた気はしたんだけど、やっぱり市場標準の納期感とも突き合わせて考えなきゃならなくてさ。調達担当との駆け引き、「いや、この便なら三週間切れそう」とか言い合う瞬間とか、なんだろう、不毛なのに妙な充実感もある。不思議だな。
正直、その場しのぎっぽく見えるんだけど――まあ実際その通りだった時期も多かったし――でも自主的な品質検証サイクルを回しておけば、不安定さは多少抑え込めた気がする。例えばテスト車両から拾った数値データで微調整する仕組みなんかね。ま、それでも完全には安心できないんだけど…。
予算とか納期に縛られてる状況で柔軟に動くには、大げさな仕組みより小回り利く工夫や現場裁量こそ効いてくると思うんだよ。いや、本当なのかな…まあ、自分はそう信じてる。
じゃあどうしたかというと、市販の汎用ケーブルをうまく混ぜて使ったりして、とりあえず全体コストを七割くらいまで落としてみたわけ。それで一息ついた気はしたんだけど、やっぱり市場標準の納期感とも突き合わせて考えなきゃならなくてさ。調達担当との駆け引き、「いや、この便なら三週間切れそう」とか言い合う瞬間とか、なんだろう、不毛なのに妙な充実感もある。不思議だな。
正直、その場しのぎっぽく見えるんだけど――まあ実際その通りだった時期も多かったし――でも自主的な品質検証サイクルを回しておけば、不安定さは多少抑え込めた気がする。例えばテスト車両から拾った数値データで微調整する仕組みなんかね。ま、それでも完全には安心できないんだけど…。
予算とか納期に縛られてる状況で柔軟に動くには、大げさな仕組みより小回り利く工夫や現場裁量こそ効いてくると思うんだよ。いや、本当なのかな…まあ、自分はそう信じてる。
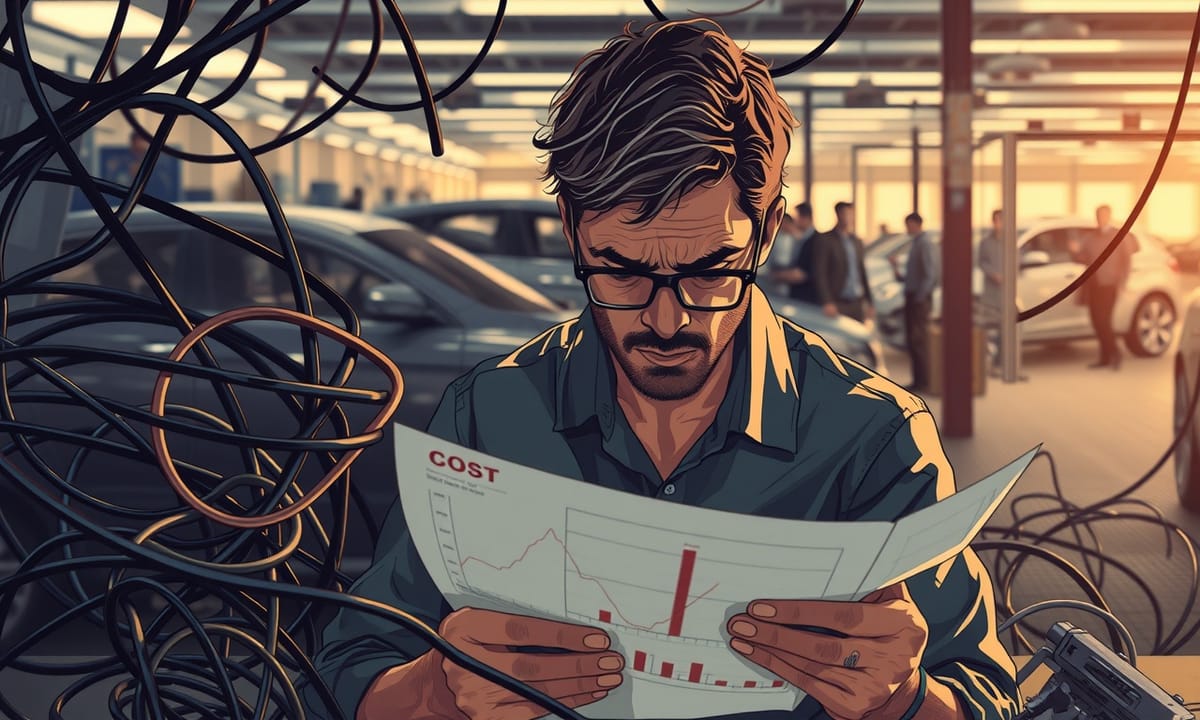
配線ミスで焼損…華麗な見た目に隠れた落とし穴再考
配線取り回しって、なんか「どうせ見えない場所だし、まあ後で考えればいいや」みたいに扱われがちなんだけど――いや、それ本当に大丈夫かなって思う。実際の現場では、この油断が地味に痛いトラブルを引き寄せたりするんだよなあ。うーん、放熱処理も同じでさ。設計段階でスペースや空気の流れをろくに確保しないままディスプレイ周りを組み立てると、あとから「何これ!?」ってぐらい局所的な過熱とか寿命短縮につながっちゃった事例が、自動車技術会(近年発表)でもちゃんと報告されてる。
…ああ、つい見た目ばっか気にして外観重視しすぎることあるよね。でも、そのせいで内部インフラがおざなりになって、最終段階で「しまった!」となるケースも決して珍しくはない。ま、いいか、と言いたくなるけど、本当は全体として美観と機能性、そのバランス感覚をどこで取るのか――そこが開発者にはずっと問われ続ける、本質的な課題なのかもしれないね。
…ああ、つい見た目ばっか気にして外観重視しすぎることあるよね。でも、そのせいで内部インフラがおざなりになって、最終段階で「しまった!」となるケースも決して珍しくはない。ま、いいか、と言いたくなるけど、本当は全体として美観と機能性、そのバランス感覚をどこで取るのか――そこが開発者にはずっと問われ続ける、本質的な課題なのかもしれないね。
老舗vsスタートアップ 評価指標ズレが招く摩擦劇
「長期的な部品供給体制は、完成車メーカーにとって不可欠だ」と大手の技術責任者が語っていた。うーん、まあ、それも一理あるよね。でもさ、その一方でスタートアップ系サプライヤーの担当者からは「市場変化への柔軟対応こそが競争力に直結する」っていう声が、けっこう聞こえてくるんだ。ま、いいか。やっぱりどちらにも事情がある。
たとえば、大手はグローバルQA基準をものすごく重視してるらしい。全工程で将来十年以上の安定運用を見据えた評価項目を採用する傾向、と言われているし…。でも実はそうでもなくて、新興勢力になると独自性強めのプロトタイプ開発とか、短期間での仕様変更提案なんかを全面に押し出してきたりもする。あれ?これどっちが正しいとかないな。
そういう価値観の違いから認識ズレとか意思疎通上の課題が浮き彫りになっている――自動車技術会・近年発表によればだけど。本筋戻すと、こうしたギャップを事前に把握しておくことは、双方どちらの立場であれ戦略設計上ひとつのヒントになるんじゃないかなと思うんだよね。
たとえば、大手はグローバルQA基準をものすごく重視してるらしい。全工程で将来十年以上の安定運用を見据えた評価項目を採用する傾向、と言われているし…。でも実はそうでもなくて、新興勢力になると独自性強めのプロトタイプ開発とか、短期間での仕様変更提案なんかを全面に押し出してきたりもする。あれ?これどっちが正しいとかないな。
そういう価値観の違いから認識ズレとか意思疎通上の課題が浮き彫りになっている――自動車技術会・近年発表によればだけど。本筋戻すと、こうしたギャップを事前に把握しておくことは、双方どちらの立場であれ戦略設計上ひとつのヒントになるんじゃないかなと思うんだよね。
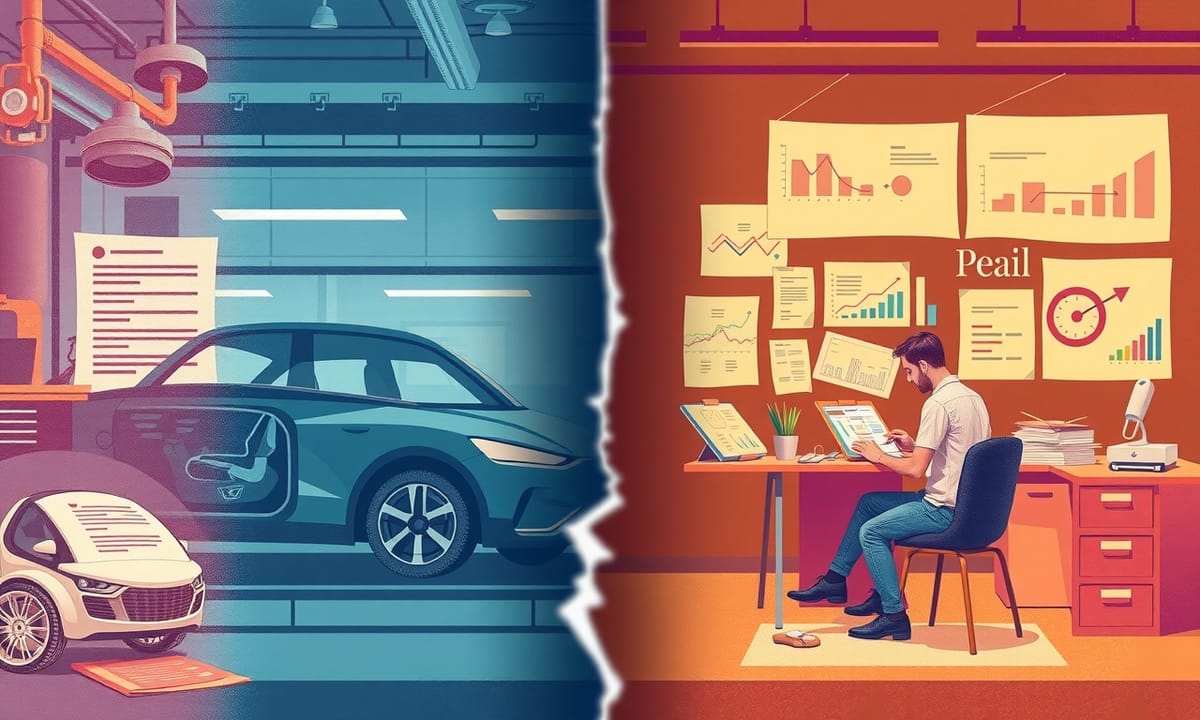
冬も要注意 曲面ダッシュ設置手順と温度管理ポイント
作業を始める前に、どこに仮固定するかっていうのを決める手順が必要不可欠なんだよね、とベテランの技術者がぽつりと漏らしていた気がする。うーん、これ別に面倒とかじゃなくて――いや、ちょっとだけ億劫かもな…でも本当に大事だよ。それからフレキシブルOLEDについては最小曲率半径を絶対守らないとまずいんだってさ。ぐっと曲げようとして変な折れ目できたり、ダッシュボードのカーブに沿わせたつもりで歪み出してしまったら悲劇だから注意深く進めたいところ。ま、途中で「あれ?」と我ながら確認したくなる瞬間あるけど、それ無視しないほうがいい。
さて次は配線を仮配置する段階になる。位置とか通し方…意外とここで迷うんだよな、自分だったら何度かやり直す気がしてならない。でもまあそこは冷静によく見ておけば問題ないと思う、多分。あと冬季など低温環境では表面クラックのリスクも報告されてたっけ(車両整備現場・昨年度観察)。ああそういえば、一時的な加温とか温度管理って面倒そうだけど重要みたい。本筋戻ると、それがチェック工程として推奨されている理由なんだろうね。
最後にはきっちり本締め作業やるべきなんだけど、その際にも一連の流れごとに確認を怠らず進めれば、おそらく良い結果につながるかな、と自分では思っている。一息入れてから振り返って見ること、大事かも…。
さて次は配線を仮配置する段階になる。位置とか通し方…意外とここで迷うんだよな、自分だったら何度かやり直す気がしてならない。でもまあそこは冷静によく見ておけば問題ないと思う、多分。あと冬季など低温環境では表面クラックのリスクも報告されてたっけ(車両整備現場・昨年度観察)。ああそういえば、一時的な加温とか温度管理って面倒そうだけど重要みたい。本筋戻ると、それがチェック工程として推奨されている理由なんだろうね。
最後にはきっちり本締め作業やるべきなんだけど、その際にも一連の流れごとに確認を怠らず進めれば、おそらく良い結果につながるかな、と自分では思っている。一息入れてから振り返って見ること、大事かも…。
美しいUIは罠?組織心理とヒューマンエラー対策考察
「UIが綺麗ならUXも良くなる」って、なぜか現場ではそのまま通じないこと、多いんだよね。えっと、この間も考えてたけど——ああ、話が逸れそう。戻るね。実際、自動車系メーカーの直近年度で、「機能を盛り込みすぎた表示領域による混乱」が七十件以上報告されたらしい。それを聞いた時、へぇ…そんなに多いんだ、とちょっと驚いた自分がいる。でもまあ、それだけじゃなくてさ、他社事例ばかりに目を向けちゃって、自信喪失しやすくなる話も結構耳にするよね。「また間違えた」と落ち込む人とか。
特に初心者の場合だけど、密集したタッチパネルで誤操作した経験、一度や二度じゃ済まないらしいっていう声も横からちらほら聞こえる。うーん、自分自身にも思い当たる節はあるかな…いや、今はその話じゃなかった。この心理的な落差とか組織内の「正解依存」、それが小さなミスや判断の遅れにつながる場面って、本当に案外多い気がして仕方ない。ま、いいか。
特に初心者の場合だけど、密集したタッチパネルで誤操作した経験、一度や二度じゃ済まないらしいっていう声も横からちらほら聞こえる。うーん、自分自身にも思い当たる節はあるかな…いや、今はその話じゃなかった。この心理的な落差とか組織内の「正解依存」、それが小さなミスや判断の遅れにつながる場面って、本当に案外多い気がして仕方ない。ま、いいか。
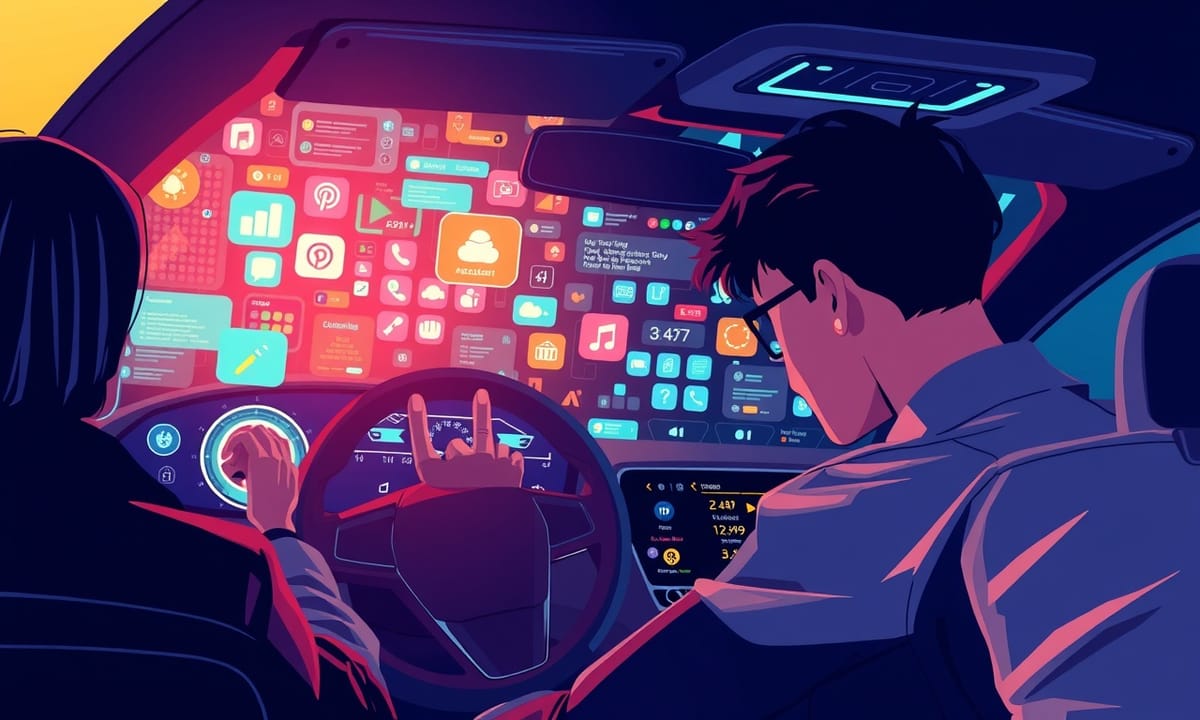
西欧は情熱重視、日本は安全主義―インテリア進化史の裏側
自動車のインテリアって、振り返ると…いや、ちょっと待って、どこまで遡ればいいんだろう。まあ、日本とか韓国のOEMは、安全性を重視してきたって言われてる。うーん、それに対して西欧の高級車界隈では、エモーションとかブランド体験みたいなものに価値を置いてる傾向が強いらしくて。たぶんね、その辺の文化差ってディスプレイの配置や操作系統──あ、時々あれ不便だよね、とか思いながらも──設計方針にも滲み出てるような気がする。
でさ、直近数年になると、自動運転技術がじわじわ浸透してきたりAR統合UIが発展したせいで、ワイド一体型ディスプレイへの需要も伸びてるっぽい。そうそう、中国メーカーによるコスト競争もあるし、その影響で価格面でも大きく風向きが変わり始めている感じなんだよなぁ。ま、今更だけど…。
この状況下では各市場ごとの技術選択やデザイン潮流をちゃんと細かく把握しておかないと、「え?そんなつもりじゃ…」みたいな導入判断ミスのリスクもあるんだっていう話。でも実際、次の三〜五年くらいは新規モデル投入や技術刷新が続々起こりそうな見通しとも聞くから、本当に市場動向には目を凝らしておいたほうが良さそう。ま、いいか。でも気になるよね…。
でさ、直近数年になると、自動運転技術がじわじわ浸透してきたりAR統合UIが発展したせいで、ワイド一体型ディスプレイへの需要も伸びてるっぽい。そうそう、中国メーカーによるコスト競争もあるし、その影響で価格面でも大きく風向きが変わり始めている感じなんだよなぁ。ま、今更だけど…。
この状況下では各市場ごとの技術選択やデザイン潮流をちゃんと細かく把握しておかないと、「え?そんなつもりじゃ…」みたいな導入判断ミスのリスクもあるんだっていう話。でも実際、次の三〜五年くらいは新規モデル投入や技術刷新が続々起こりそうな見通しとも聞くから、本当に市場動向には目を凝らしておいたほうが良さそう。ま、いいか。でも気になるよね…。
『何を妥協し、何を譲らぬか』現場発ユースケース発想のすすめ
「どこまで妥協できるのか、逆に何があっても絶対に譲れない部分はどこなのか——うーん、こういう線引きって意外と早めに決めておいた方が楽なんだよね。いや、ちょっと話それるけど、自分でも昔は『まあ何とかなるでしょ』って曖昧なまま進めてたことが多くて…結局トラブった記憶しかない。でも本筋戻すと、関係者間でそうしたポイントをはっきりさせてから仕様検討に入るのが肝要らしい。その後も設計や調達、それから現場運用まで、とにかく最初から最後まで現場の声をちゃんと反映し続ける流れが望ましい、とされている。ま、いいか。
具体的には初期案の時点で即座に突っ走らず、一度試作してみたり、小さい規模で実証実験を何度もやったりすることで——えっと、思いもしなかったような隠れ課題を拾える可能性がある。それによって必要なら評価基準や指標そのものを見直す覚悟も持つべきなんじゃないかなと思うわけです。技術だけじゃなくコスト面とか、人間工学的観点も交えて複数視点でバランス考える姿勢、大事…だけど全部完璧になんて無理だしね。むしろ制約だらけの状況下でも、その都度現場との認識合わせを挟みながら代替案比較して意思決定していく——そんな手法が有効だと言われているんだけど、本当のところどうなんだろう、まあ経験則的には間違いじゃない気がする。
具体的には初期案の時点で即座に突っ走らず、一度試作してみたり、小さい規模で実証実験を何度もやったりすることで——えっと、思いもしなかったような隠れ課題を拾える可能性がある。それによって必要なら評価基準や指標そのものを見直す覚悟も持つべきなんじゃないかなと思うわけです。技術だけじゃなくコスト面とか、人間工学的観点も交えて複数視点でバランス考える姿勢、大事…だけど全部完璧になんて無理だしね。むしろ制約だらけの状況下でも、その都度現場との認識合わせを挟みながら代替案比較して意思決定していく——そんな手法が有効だと言われているんだけど、本当のところどうなんだろう、まあ経験則的には間違いじゃない気がする。