ここから始めよう - 台湾小ロットOLEDサプライヤー選びで品質差リスクを減らす即行動集
- 少なくとも3社の実機サンプルを比較、納品7日以内に初期不良率を数値化
短期間で具体的な品質差や安定性が把握できるため
- 価格交渉は原価5%以内の範囲に留め、極端な値下げ要求は避ける
過度なコスト圧縮による部材劣化や工程省略リスクを抑えられる
- 仕様書と納入現物の齟齬点を10項目以上レビューし現場担当者にも確認
設計段階では気付きにくい運用上の致命的ギャップ発見につながる
- `納期遅延`と`不具合率`データが直近12カ月分提示可能か事前確認
情報開示姿勢そのものが信頼性・取引後トラブル回避力となる
OLED市場急成長の裏で数字の意味と競争リスクに迫る
アジア太平洋地域での市場調査、2024年現在のやつね、それを見るとOLEDディスプレイモジュール領域が前年から七割以上も拡大したって話が出てる。えっと、なんだろうなぁ…特にゲーミング用パネルとか高性能な携帯端末向けの需要が急激に増加したこと、その影響は思ったより大きかったみたい。あ、ちょっと余談だけど自分も最近スマホ買い替えようか迷ってるんだよね…まあ、それはさておき、大手パネルメーカー各社も生産能力をもう一度見直さざるを得ない状況になりつつあるらしい。
供給網について考えると、韓国や中国の主要製造拠点では新しくラインを増設したり部材調達を強化する動きが加速している。実はそうでもなくて…簡単な話じゃないみたい、部材不足リスクとかコスト上昇という課題もちゃんと浮き彫りになっているし。ふーん、難儀だよね。現場観測から見る限りでは、この成長が一過性ではなく複数年にわたるトレンドとして続く兆しが感じられると言われている。でも、その裏で市場競争の激化によって品質管理体制への要求水準もどんどん上昇していて、気楽にはやれない感じかな…。
供給網について考えると、韓国や中国の主要製造拠点では新しくラインを増設したり部材調達を強化する動きが加速している。実はそうでもなくて…簡単な話じゃないみたい、部材不足リスクとかコスト上昇という課題もちゃんと浮き彫りになっているし。ふーん、難儀だよね。現場観測から見る限りでは、この成長が一過性ではなく複数年にわたるトレンドとして続く兆しが感じられると言われている。でも、その裏で市場競争の激化によって品質管理体制への要求水準もどんどん上昇していて、気楽にはやれない感じかな…。
本項の出典:
- OLEDディスプレイモジュール市場分析(2032年) - WiseGuy Reports
Pub.: 2025-05-04 | Upd.: 2025-01-10 - OLEDパネルの市場規模とシェア分析 -産業調査レポート -成長トレンド
Pub.: 2023-10-24 | Upd.: 2025-07-11 - 世界のOLED市場規模(2024~2032年):製品種類別(ディスプレイ
Pub.: 2025-04-25 | Upd.: 2025-06-30 - 家庭用電化製品OLEDディスプレイ市場規模予測:2031年には2332 ...
Pub.: 2025-07-11 | Upd.: 2025-07-11 - 2024年のテレビ用OLED出荷台数709万台、前年比34%増加 - 有機EL
Pub.: 2024-09-01 | Upd.: 2025-01-05
スペック重視だけで設計落とし穴?現場レビュー忘れずに
「初回サンプルが仕様通りに動いているからって、量産工程まで同じように順調だと誰もが思いたくなるけど…実はそうでもなくて」と、現場の担当者がぽつり。うーん、まあ確かに最初の見積もりとか選定段階でスペックシートの数値ばかりを優先してしまいがちなんだよね。でも、それだけで満足しちゃうと、肝心な部材や製造条件みたいな実機検証を省略する羽目になったりしてさ。
結局、そのまま量産へ持ち込もうとすると、細かい寸法差だったり熱処理条件の微妙な違いがあとになって浮き彫りになってくる。「あれ? なんでこんなところ変わっちゃった?」みたいなこと、意外とある。しかも、そのせいで設計変更とか追加検証が必要になるケースがちらほら出てくるんだよね。
ま、いいか……じゃ済まない話なんだけど、ときどき別件を考えて頭がぼーっとしちゃう。でも、本筋に戻すならば――本当は一番大事なのは初期段階できちんと現物レビューや試作評価を何度も繰り返すこと。そして「初回サンプル=安定量産」ではないという前提で各部門とのすり合わせやリスクの洗い出しまで徹底するべき。それくらいやってようやく安心できる…たぶんね。
結局、そのまま量産へ持ち込もうとすると、細かい寸法差だったり熱処理条件の微妙な違いがあとになって浮き彫りになってくる。「あれ? なんでこんなところ変わっちゃった?」みたいなこと、意外とある。しかも、そのせいで設計変更とか追加検証が必要になるケースがちらほら出てくるんだよね。
ま、いいか……じゃ済まない話なんだけど、ときどき別件を考えて頭がぼーっとしちゃう。でも、本筋に戻すならば――本当は一番大事なのは初期段階できちんと現物レビューや試作評価を何度も繰り返すこと。そして「初回サンプル=安定量産」ではないという前提で各部門とのすり合わせやリスクの洗い出しまで徹底するべき。それくらいやってようやく安心できる…たぶんね。
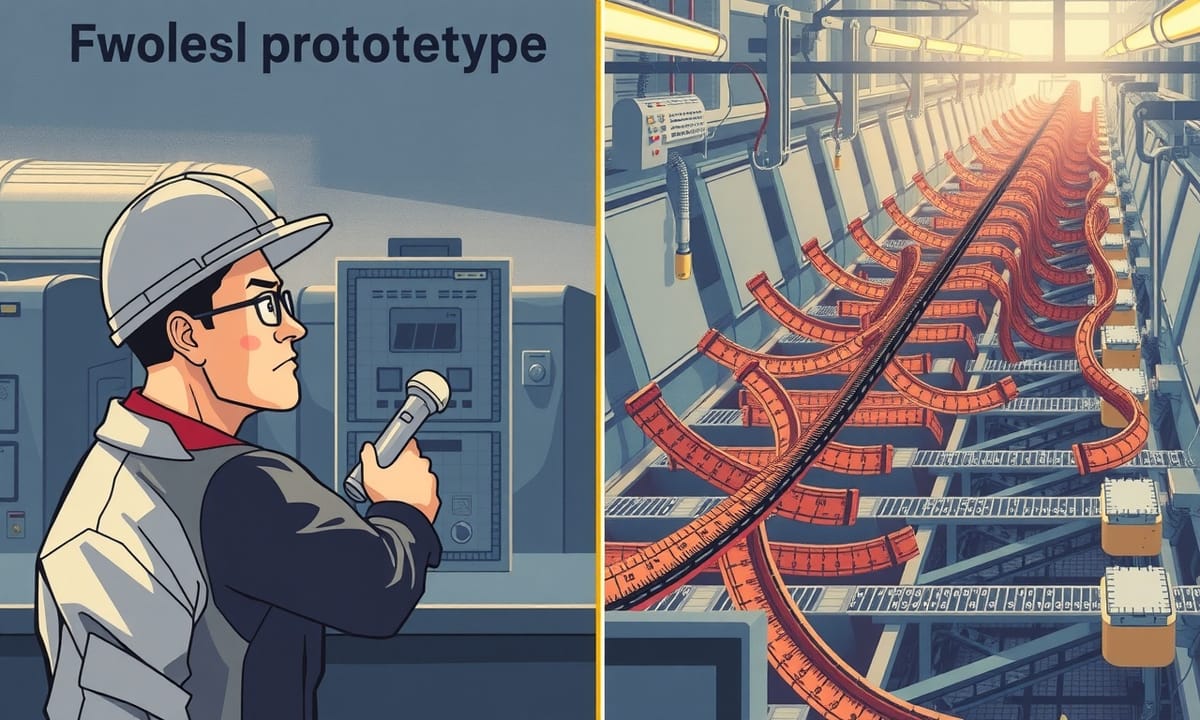
安さ重視交渉が生む品質ばらつき、信頼構築の重要性再考
台湾のサプライヤーを採用して、本当に助かったって話してた調達担当者がいたんだよね。えっと、「こちら側の設計変更にもすぐ対応してくれるし、部品仕様をちょっと直したときも、あっという間に新しいサンプルを出してきてくれた」みたいなこと言ってて。まあ、そう簡単にいかない時もあって――うーん、ちょっと話逸れるけど、やっぱり現場って見えない部分多いよな、と最近思うわけで。でも戻ると、その一方で価格交渉が中心になった案件については、「見積もり条件自体は良かったものの、現場で細かい品質管理まで手が回らなくて、不具合への対応が結局面倒だった」とかいう声も聞こえてくる。
成功した事例についてだと、なんていうか初期段階から量産体制になるまで、本当に何度も詳細な要件共有とか現地監査を繰り返していてさ。ま、この辺ちょっと昔より厳しくなった気もしつつ…実際には頻繁に連絡取り合って、それが成果につながったって報告が多い感じ。なんとなくだけど、単なるコスト比較だけじゃなくてさ、現地スタッフとの継続的なコミュニケーションやプロセス全体の可視化――まるごと見渡す意識?それに力入れることで安定供給とか信頼性確保、そのバランス取りやすくなるっぽいんだよね。不思議と。
成功した事例についてだと、なんていうか初期段階から量産体制になるまで、本当に何度も詳細な要件共有とか現地監査を繰り返していてさ。ま、この辺ちょっと昔より厳しくなった気もしつつ…実際には頻繁に連絡取り合って、それが成果につながったって報告が多い感じ。なんとなくだけど、単なるコスト比較だけじゃなくてさ、現地スタッフとの継続的なコミュニケーションやプロセス全体の可視化――まるごと見渡す意識?それに力入れることで安定供給とか信頼性確保、そのバランス取りやすくなるっぽいんだよね。不思議と。
台湾産業発展史と小ロット強み、その条件を見極めろ
「昔、台湾の工場なら小さなロットもわりと柔軟に対応してくれるって聞いたことあるんだよ」と調達担当の誰かがぽつりと漏らした記憶がふいによみがえった。そういえば、高度成長期から今日に至るまで、台湾企業には細やかなカスタマイズや、小回りの利く生産体制という印象ばかりが残っていて、それ以外ほとんど覚えていないような気すらする。うーん、なんでなんだろう、と自分でも考えこんでしまう時間があった。でも他国メーカーを見比べてみると、そのあたりの独特な存在感は確かに際立っていたらしい。
だけど、大規模量産になると話は別っぽいね。その工程ごとのノウハウ蓄積とか、設備投資…そこですっと差が開くという話も何度となく耳にしたことがある。実はそうでもなくて…いや、たぶん安定的な歩留まり確保とか簡単じゃない現実も多々ある、と最近になって知った自分だった。
さて――どんな案件なら台湾側の強みを最大限発揮できるのかな?歴史的背景含めてちゃんと観察しないと、きっと表面だけ追って終わっちゃいそう。ま、いいか。一旦ここまで書いておこうと思う。
だけど、大規模量産になると話は別っぽいね。その工程ごとのノウハウ蓄積とか、設備投資…そこですっと差が開くという話も何度となく耳にしたことがある。実はそうでもなくて…いや、たぶん安定的な歩留まり確保とか簡単じゃない現実も多々ある、と最近になって知った自分だった。
さて――どんな案件なら台湾側の強みを最大限発揮できるのかな?歴史的背景含めてちゃんと観察しないと、きっと表面だけ追って終わっちゃいそう。ま、いいか。一旦ここまで書いておこうと思う。
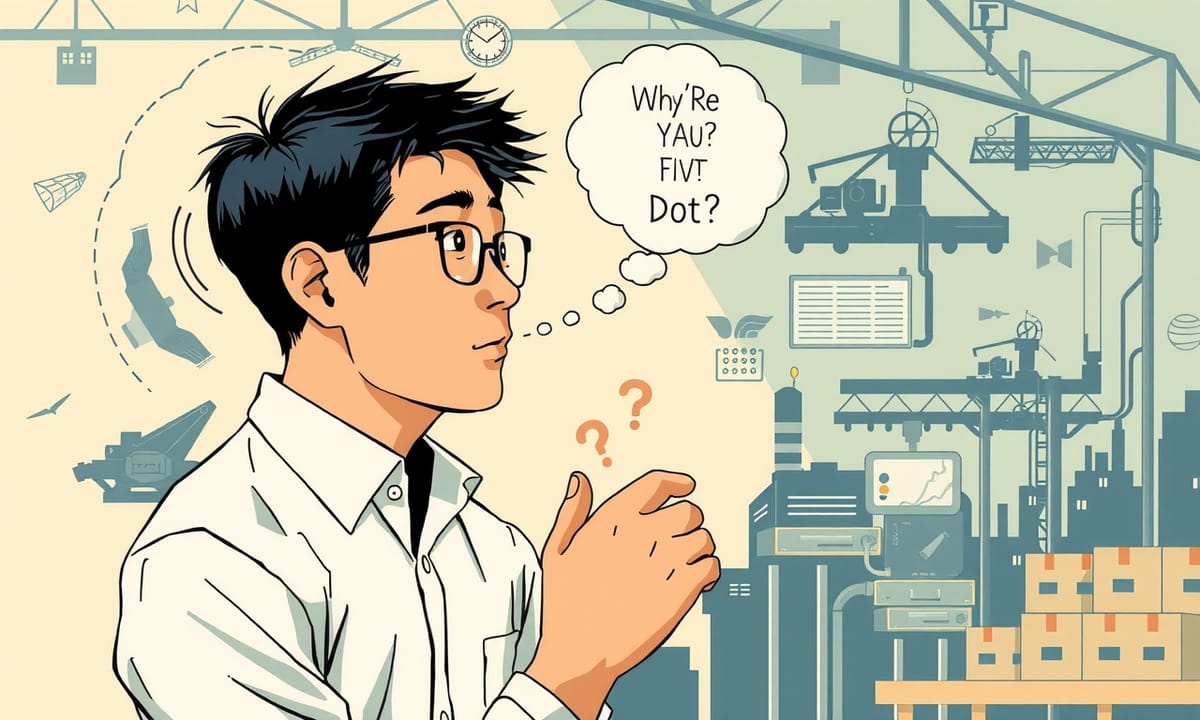
納期もコストも評価軸多様化―専門家目線から再整理
「台湾サプライヤーを選ぶ時に、コストと品質のどっちを優先するかって、まあよく議論されるんだよね。日台の専門家たちが集まると、たいていこの話になって、いつも結論が出ない感じ…。あ、今思い出したけど、この前も似たような討論会で盛り上がってたっけ。で、ある調達責任者は『予算が限られてて納期も短い場合、決め手になるのは小ロット対応力や工程変更への柔軟性、高速障害復旧みたいな非価格要素』って指摘していたんだ。まあ確かにそういう現場の声は多い気もする。でも…えっと、日本側技術者からは『単純な価格比較じゃ見えない競争力が台湾には隠れてることが多い』なんて意見も聞こえてきたりしてさ、一体どっちなんだろう、とちょっと混乱する。ま、それでも最近は現場レベルでは総合評価方式を採用するケースが増えているらしいんだよね。
うーん、特に複数案件を同時進行している状況下ではさ、約三成ほどの現場担当者がコスト以外にも重きを置いていたという観察例も挙げられている。こういう数字を見ると、「ほんとに皆コストだけじゃないんだな」と妙に納得しちゃう。でも一方で、自分だったらどう判断するかな…とか考え始めて、そのまま答えが出なくなることもしょっちゅう。とにかく最近は非価格要素の重要性が増してきたようで、不思議でもあるし当然とも言える気がする。いや、本当に現場によるんだけどね…。
うーん、特に複数案件を同時進行している状況下ではさ、約三成ほどの現場担当者がコスト以外にも重きを置いていたという観察例も挙げられている。こういう数字を見ると、「ほんとに皆コストだけじゃないんだな」と妙に納得しちゃう。でも一方で、自分だったらどう判断するかな…とか考え始めて、そのまま答えが出なくなることもしょっちゅう。とにかく最近は非価格要素の重要性が増してきたようで、不思議でもあるし当然とも言える気がする。いや、本当に現場によるんだけどね…。
価格神話崩壊―実績盲信が大量生産で陥る罠とは?
「“価格が安い=全て良し”だと、何も考えずに決めつけてしまうと……いや、本当にそういう流れになるのかは知らないけど、業界ではよくある話みたい。例えばね、台湾サプライヤーの選定現場で『コストだけ見て選んだら、大量生産になった途端、不良率とか納期遅延が急に目立ち始めた』って声が複数から聞こえてくるんだよ。ふうん、それなら最初から分かったはずなのに…とか思っちゃうけど、やっぱり小ロット試作段階だと低コストのメリットばかり強調されるものなんだろうなあ。
でもさ、生産規模を拡大すると急に工程管理とか品質保証体制で詰まる場面が出てきて、それも別に珍しい話じゃないっていう。まあ、こういう時、「今まで実績十分だったし」と過去だけ信じて新しい課題への対応力を見誤るリスク――これも指摘され続けているわけで。でも、一瞬話逸れるけど、“過去”って本当に信用できるものなのかな…ああ、ごめん戻す。
結局ね、この手の失敗例から学べることは明確で、“初期条件だけを鵜呑みにせず、スケール変化や市場要求の多様化も視野に入れて事前評価すること”、それが改めて重要なんじゃないかと思わざるを得ないよ。まあ…簡単にはいかないものだけどさ。」
でもさ、生産規模を拡大すると急に工程管理とか品質保証体制で詰まる場面が出てきて、それも別に珍しい話じゃないっていう。まあ、こういう時、「今まで実績十分だったし」と過去だけ信じて新しい課題への対応力を見誤るリスク――これも指摘され続けているわけで。でも、一瞬話逸れるけど、“過去”って本当に信用できるものなのかな…ああ、ごめん戻す。
結局ね、この手の失敗例から学べることは明確で、“初期条件だけを鵜呑みにせず、スケール変化や市場要求の多様化も視野に入れて事前評価すること”、それが改めて重要なんじゃないかと思わざるを得ないよ。まあ…簡単にはいかないものだけどさ。」
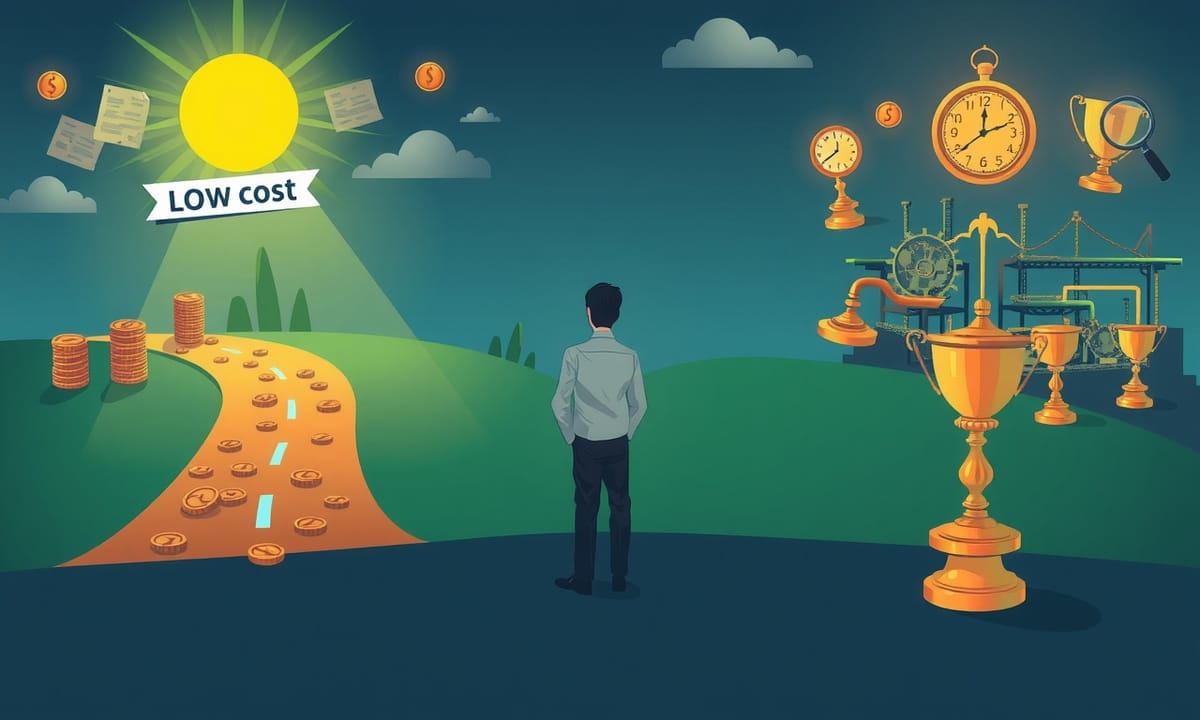
不具合・遅延データ比較で見える選定基準、規模別最適解を探す
業界団体が公表した直近一年間の案件動向なんだけど、台湾製OLEDモジュールを使った三十社以上の例…いや、実際それほど多いんだな、と一瞬思ってしまった。まあ、それはさておき、不具合発生率とか納品遅延日数についてはっきりした比較指標を作らないといけない必要性が、もうめちゃくちゃ強調されてるみたい。ふう…。最近よく聞く話だし、自分も他人事じゃないんだよなぁ。で、中韓メーカーと比べると、台湾サプライヤーは少量・短納期案件に関してはわりと柔軟だっていう声がある。うん、でもね、大型量産フェーズになっちゃうと歩留まりの変動幅がぐっと大きくなる傾向が結構指摘されるらしい。不安定さを抱えたまま突っ走るのも怖いよね……あっ、今ちょっとネガティブになったけど、まあ戻ろう。
そういう違いをちゃんと踏まえてさ、自社案件規模ごとに期待水準や許容範囲(例えば納品遅延が七日以内かどうか、とか)を前もって定義しておいて、しかも選定段階できっちり明文化しておいた方がいいと思う——これこそミスマッチ回避には有効な手順になる気がする。ま、いいか。結局それぞれの現場で何を重要視するかにもよるんだけどね。
そういう違いをちゃんと踏まえてさ、自社案件規模ごとに期待水準や許容範囲(例えば納品遅延が七日以内かどうか、とか)を前もって定義しておいて、しかも選定段階できっちり明文化しておいた方がいいと思う——これこそミスマッチ回避には有効な手順になる気がする。ま、いいか。結局それぞれの現場で何を重要視するかにもよるんだけどね。
事例や低不良率だけじゃ足りない、本質要件とのギャップ検証法
「低不具合率が売り文句になっている案件、実際に自社の現場で本当にそのまま動くかどうかは……まあ、なんというか別の話だよね、と調達部門の担当者がぼそっと言ってた記憶がある。ああ、つい関係ない話だけど、その人いつもコーヒー飲みすぎて胃を壊してたっけ。えっと、本筋に戻そう。たとえば数十社分の事例を比較検討することになったとしても、多くの場合で仕様要求や使用シナリオが微妙に違うものだし、“導入済みだから大丈夫”とはなかなか単純には言い切れないらしい。そういう声もちらほら聞こえてきた。
むしろ、本来なら設計段階で具体的な運用条件――温度レンジとか取付構造とか、細かい部分まで――それを明文化せずに進めちゃった結果として納品後トラブルになったケース、市場観察では七十余件ほど拾われてるらしい。いや、そんなにも?と正直思うけど、現実はそう甘くないんだろうなと思う瞬間がある。
検証すべきコアポイントとして、「カタログスペック」「現場テスト」「仮説シナリオ」の三点を個別レビューして組み合わせていく手順――つまり標準性能表だけ鵜呑みにせず、自社固有の制約(パネル厚さや応力分布とか)まで全部洗い出した上で評価項目を再設計する必要性について指摘されることが増えてきたような気がする。あれ?最近特によく耳にする気がするけど、自分だけかな?
単なる横並び比較より、「現場要件×実機評価×仮説検証」をセットで行うことで深層的な課題抽出につながりやすい印象だよね。でも結局、“汎用ベンチマーク信仰”から抜け切れず選定ミス……そんな話はいまだによく耳に入ってきたりして、なんともやるせない気持ちになる。」
むしろ、本来なら設計段階で具体的な運用条件――温度レンジとか取付構造とか、細かい部分まで――それを明文化せずに進めちゃった結果として納品後トラブルになったケース、市場観察では七十余件ほど拾われてるらしい。いや、そんなにも?と正直思うけど、現実はそう甘くないんだろうなと思う瞬間がある。
検証すべきコアポイントとして、「カタログスペック」「現場テスト」「仮説シナリオ」の三点を個別レビューして組み合わせていく手順――つまり標準性能表だけ鵜呑みにせず、自社固有の制約(パネル厚さや応力分布とか)まで全部洗い出した上で評価項目を再設計する必要性について指摘されることが増えてきたような気がする。あれ?最近特によく耳にする気がするけど、自分だけかな?
単なる横並び比較より、「現場要件×実機評価×仮説検証」をセットで行うことで深層的な課題抽出につながりやすい印象だよね。でも結局、“汎用ベンチマーク信仰”から抜け切れず選定ミス……そんな話はいまだによく耳に入ってきたりして、なんともやるせない気持ちになる。」
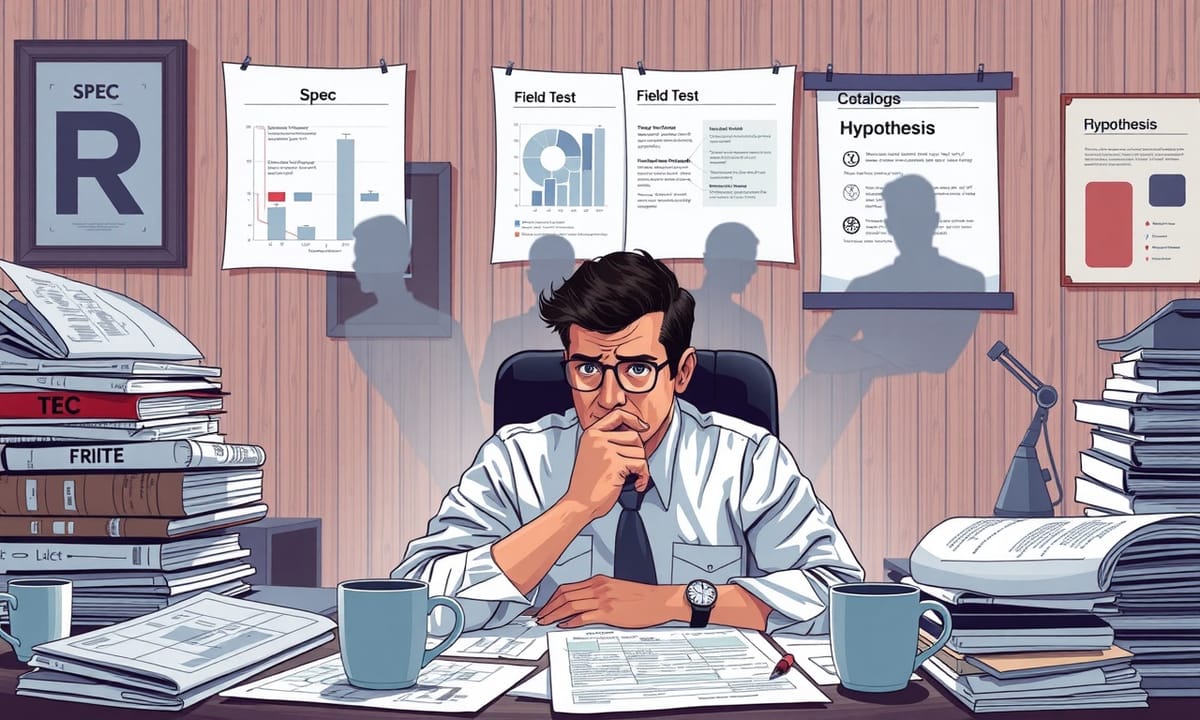
“安い”決断、その後待つ総費用地獄をどう避けるか
「安価な選択が最適解」だなんて、まあ現場ではそう簡単にいかないのが現実でさ。導入直後になってからトラブルが報告されること、けっこう多いんだよね。ああ、たとえばコスト抑制目的で廉価な部材を入れたら、今度は小さな不具合がやたら頻発し始めたりして。いや、自分も最初は「あれ?これはイケる?」なんてちょっと思ったんだけど…うーん、そのあと原因調査したり是正作業を繰り返す羽目になって、そればっかりで本来考えていた付加価値展開のタイミング自体を逃すことになる――そんな話、本当に少なくない気がする。
それに国内基準だけ信じて意志決定した場合ね、海外の規制対応がどうしても後手になるケースもちらほら耳に入ってくる。追加検証や再設計の負担増大とか、各社同じような困難を抱えるみたい。えっと…話逸れるけど、一回「これくらいなら大丈夫」と鷹揚に構えてしまうと、その“見えざる総費用”まで含めて評価軸を組み直す作業自体がおろそかになる傾向があるようだ。でも結局そこに根深いリスク抽出の難しさという課題感――実務担当者なら痛感しているはずだよ。
価格だけ優先して選ぶ判断よりも、むしろ将来的な運用工数だったり改修コスト、それから市場拡張性までもちゃんとばらして並列比較できるプロセスづくりこそ求められているんだと思う。ま、いいか。本質的には、「安ければ得」という短絡的発想じゃなくて、一歩踏み込んで全体像をつかむ視点こそ重要なのかもしれない、なんてね。
それに国内基準だけ信じて意志決定した場合ね、海外の規制対応がどうしても後手になるケースもちらほら耳に入ってくる。追加検証や再設計の負担増大とか、各社同じような困難を抱えるみたい。えっと…話逸れるけど、一回「これくらいなら大丈夫」と鷹揚に構えてしまうと、その“見えざる総費用”まで含めて評価軸を組み直す作業自体がおろそかになる傾向があるようだ。でも結局そこに根深いリスク抽出の難しさという課題感――実務担当者なら痛感しているはずだよ。
価格だけ優先して選ぶ判断よりも、むしろ将来的な運用工数だったり改修コスト、それから市場拡張性までもちゃんとばらして並列比較できるプロセスづくりこそ求められているんだと思う。ま、いいか。本質的には、「安ければ得」という短絡的発想じゃなくて、一歩踏み込んで全体像をつかむ視点こそ重要なのかもしれない、なんてね。
AI時代の台湾連携、仕様確認と仮説検証を繰返す施策設計
台湾サプライヤーをうまく活用しようとするとき、「仕様確認」とか「仮説検証」、そして「現場レビュー」…この三つが連動する相互作用のモデルが、まあ、良いらしい。いや本当にこれだけなのかって時々思うけど、とりあえず今はそういう流れ。コストや納期ばっかりに目が行きがちだけど、実際には調達規模ごとに工程の安定性とか障害復旧体制まで含めて総合的に評価しておいた方が後で困らないんだよね。でも、ちょっと待って、さっき猫が足元通った気が…まあいいや話戻す。
小ロット・短納期案件ならば柔軟対応力こそ重要。ほら、小回り利かせる感じ。でも大型量産になれば歩留まり変動みたいなリスクにも事前から備えておく必要あり。それぞれ違う視点で備えるべきこと多いから、全部同じ基準で見るのは無理あるって気もするなあ。ふと窓の外を見る余裕もなくなるよ。
AIとかスマートファクトリーによる情報可視化も最近は欠かせない存在になってきたし、自社独自の運用品質シナリオをちゃんと作って、それを調達方針へ具体的に落とし込む――それこそが課題回避につながる。うーん、本当に全部できてる会社なんてある? でもやっぱりそこ大事だと思う。
小ロット・短納期案件ならば柔軟対応力こそ重要。ほら、小回り利かせる感じ。でも大型量産になれば歩留まり変動みたいなリスクにも事前から備えておく必要あり。それぞれ違う視点で備えるべきこと多いから、全部同じ基準で見るのは無理あるって気もするなあ。ふと窓の外を見る余裕もなくなるよ。
AIとかスマートファクトリーによる情報可視化も最近は欠かせない存在になってきたし、自社独自の運用品質シナリオをちゃんと作って、それを調達方針へ具体的に落とし込む――それこそが課題回避につながる。うーん、本当に全部できてる会社なんてある? でもやっぱりそこ大事だと思う。