ここから始めよう - 台湾OLEDモジュール調達のリスクを最小化し、現場で失敗しない選定力を強化
- 見積依頼時に主要仕様・品質条件を10項目以上明記する
曖昧な要求が不良や納期遅延の温床となるため、要件明確化でトラブル7割減
- サンプル評価は最低3社×5台以上でMini Field Test実施
現場環境下テストにより初期故障率や歩留まり差異を数値で把握できる
- 価格だけでなくISO9001など認証取得状況も必ず確認
"安い=高リスク"回避、品質管理体制の有無が量産後のクレーム発生率低下につながる
- `納期短縮`提案時は標準納期比30%以上早い場合のみ追加検証フロー設ける
無理な短縮は部材調達や検査省略による重大欠陥発生リスクがあるため
現場で浮かび上がる選定リスクとMini Field Test設計
「規格書だけ見てモジュールを選んでいったせいで、量産初期にまさかのトラブルが次々と発生し始めたことがあってさ……あれ、今思い出しても胃がきゅっとする。まあ、自分が担当した案件なんだけど。うーん、そうだな、有機ELパネル(OLEDディスプレイ)の調達を始めたばかりの頃って、とりあえずサプライヤーから紙面上では合格判定もらったことでちょっと気持ち緩んじゃう。でも実際は、生産現場に入ると歩留まりや納期とか新しく頭痛くなる課題が、何故か次々顔を出す。不思議だよね、本当に。
それで私たちのチームはmini Field Testという形で、小ロットを複数社から長期間にわたり検証したんだよね。途中で別件のメール来て少し手止まっちゃったけど…いや、話戻すと、不良発生件数とか稼働安定性についても徹底的に追跡していた。これによって短期間評価じゃ見抜けないような潜在リスク――つまり後から表面化する問題なんだけど、それをわりと早めにつかみやすくなった感じかな。
それと、「一度合格=もう安心」みたいな誤解は避けたかったので、そのためにも定期的にサンプル再テストを続けている。ま、大変だけど仕方ない。それでもやっぱり油断できない部分、多い気がするよね…。
それで私たちのチームはmini Field Testという形で、小ロットを複数社から長期間にわたり検証したんだよね。途中で別件のメール来て少し手止まっちゃったけど…いや、話戻すと、不良発生件数とか稼働安定性についても徹底的に追跡していた。これによって短期間評価じゃ見抜けないような潜在リスク――つまり後から表面化する問題なんだけど、それをわりと早めにつかみやすくなった感じかな。
それと、「一度合格=もう安心」みたいな誤解は避けたかったので、そのためにも定期的にサンプル再テストを続けている。ま、大変だけど仕方ない。それでもやっぱり油断できない部分、多い気がするよね…。
納期短縮神話に潜む台湾系サプライヤーの落とし穴
「台湾系サプライヤーは納期対応が迅速だと、つい信頼できるイメージを持たれがちなんだけど、実際には短納期だけに気を取られてしまって、その結果思わぬコスト増や品質リスク…ああ、なんか昨日も似た話を聞いたけど…まあ、とにかくそういう問題に直面するケースが割と多いんだよね」と専門家の方は静かに危惧している。えっと、例えばさ、台湾側で量産移行後に不具合が発生した時とか、そのフォロー体制が十分じゃなくて追加検査とか再作業とか結局必要になっちゃって、それで全体的なコストが約三割も上乗せされた例も本当にあるみたい。
うーん、西洋系サプライヤーになると逆に契約内容通り長期的な支援を重視する傾向のほうが強い印象かな、この辺り文化の溝というか認識差みたいなのが露骨になりやすいし…。いやでもそれって絶対悪いこととも言い切れないよね?担当者同士でも認識違いからクレーム処理自体複雑化しちゃったりして、「スピードさえ追えば万事解決」なんてことにはまずならないぞって指摘は今なお根強く残っている。ま、いいか。
うーん、西洋系サプライヤーになると逆に契約内容通り長期的な支援を重視する傾向のほうが強い印象かな、この辺り文化の溝というか認識差みたいなのが露骨になりやすいし…。いやでもそれって絶対悪いこととも言い切れないよね?担当者同士でも認識違いからクレーム処理自体複雑化しちゃったりして、「スピードさえ追えば万事解決」なんてことにはまずならないぞって指摘は今なお根強く残っている。ま、いいか。
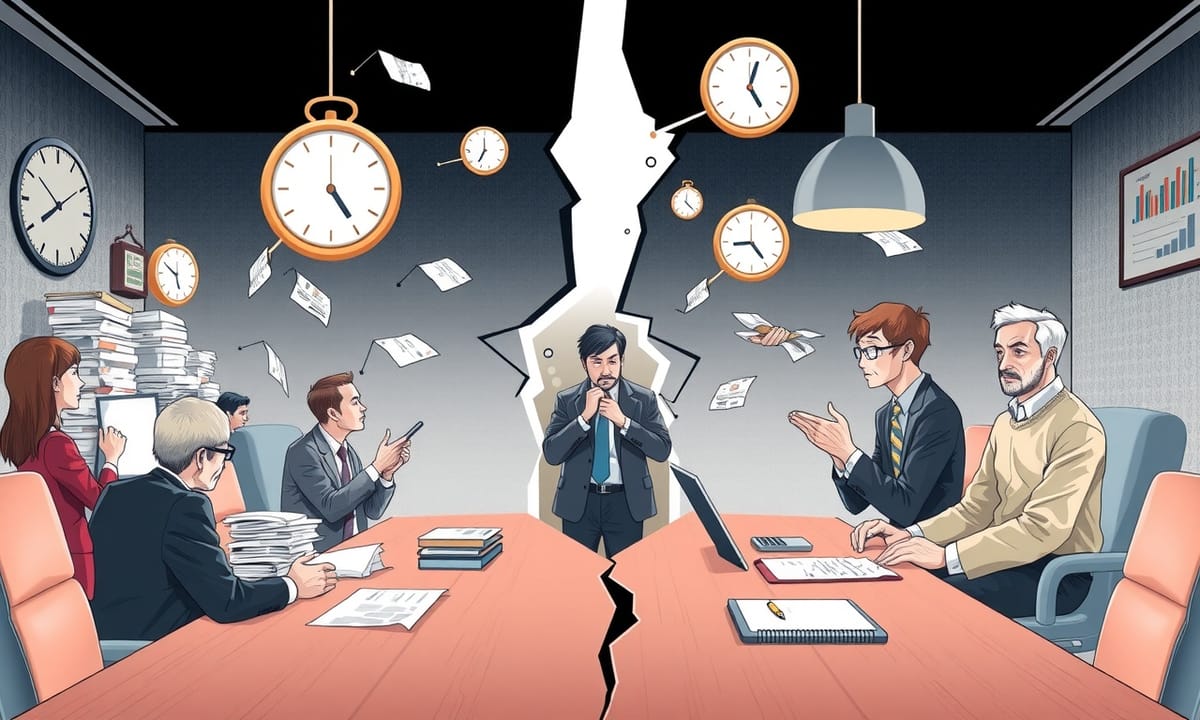
ブランドや安値だけじゃない、見逃せない供給網の罠
「“安い・有名・早い”、この三つがそろえば万事オーケー……みたいな選び方、うーん、現場じゃ実は驚くほど当たり前にされてたりするんだよね。いや、なんでそんなに単純化したがるのか……まあ誰しも分かりやすい軸を求めたくなる気持ちもあるけど。でさ、本当に大丈夫なのかなって思ったりもするわけ。
実際には、その基準だけで突っ走ると、ときどき意外な落とし穴に引っかかることが多かったりして……。例えば導入初期なんてコスト削減とかリードタイム短縮ばっかり目立つのが普通。でも、それだけ見てたら後になってアフターサポート不足とか、法規制が変わって突然供給止まっちゃうとか、「え?そこ?」みたいな問題が噴き出してくるパターン、ちらほら耳にするんだよね。ああ、それから頻繁なサプライヤー交代になると社員教育の負担だとか、新設備立上げまでの時間増加とか、余計な副次的損失まで現れてしまうこともあるし……面倒だな。
あ、話ズレちゃった?いやでも、この無駄な遠回り感こそ肝心だったりして。本筋に戻すけど――つまりさ、初期条件だけで最適解を探そうとしてしまうと、中長期では結局全体コストや事業継続性への悪影響を完全には避けられないという現実を無視できなくなる。ま、いいか。でも本当は一番重視すべき要素ってもっと複雑だったり、多角的に検証する姿勢そのものが重要なんじゃないかなぁ、と最近よく考えるんだ。
実際には、その基準だけで突っ走ると、ときどき意外な落とし穴に引っかかることが多かったりして……。例えば導入初期なんてコスト削減とかリードタイム短縮ばっかり目立つのが普通。でも、それだけ見てたら後になってアフターサポート不足とか、法規制が変わって突然供給止まっちゃうとか、「え?そこ?」みたいな問題が噴き出してくるパターン、ちらほら耳にするんだよね。ああ、それから頻繁なサプライヤー交代になると社員教育の負担だとか、新設備立上げまでの時間増加とか、余計な副次的損失まで現れてしまうこともあるし……面倒だな。
あ、話ズレちゃった?いやでも、この無駄な遠回り感こそ肝心だったりして。本筋に戻すけど――つまりさ、初期条件だけで最適解を探そうとしてしまうと、中長期では結局全体コストや事業継続性への悪影響を完全には避けられないという現実を無視できなくなる。ま、いいか。でも本当は一番重視すべき要素ってもっと複雑だったり、多角的に検証する姿勢そのものが重要なんじゃないかなぁ、と最近よく考えるんだ。
調達現場で絡み合う地政学・技術継承・連鎖停止リスク
「“地政学リスクで原材料が突然途切れたこと、経験ありませんか?”と、ある購買担当者がぼそっと語っていた。ああ、ほんと現場は大変だよね。新技術の共同開発なんて特にそう、えっと引継ぎ資料も残らずに気づけばすべて現場任せ…いや、それどころか、ノウハウ自体がふっと消えてしまうことも珍しくない。ま、いいか。でも話を戻すけど。
サプライチェーン全体を見渡してみるとさ、不思議なほど複雑に七十以上もの部材や設備が絡み合ってる。その一つだけでもつまずくと、とたんに連鎖的に製造停止になった事例も実際聞くし――うーん、自分だったら心配で眠れなくなるかも。ちょっと余談だけど、この前同僚ともそんな話になったっけ。
最近は、「仕様とか運用っていったいどこまで標準化・文書化しておけば安心できるの?」という声をちらほら耳にするようになった気がする。形式知として運用ノウハウ含め橋渡しできれば理想だけど、それもまた手間ばっかり増える感じで…まあ、結局どうしてもしんどさは付きまとうよね。
サプライチェーン全体を見渡してみるとさ、不思議なほど複雑に七十以上もの部材や設備が絡み合ってる。その一つだけでもつまずくと、とたんに連鎖的に製造停止になった事例も実際聞くし――うーん、自分だったら心配で眠れなくなるかも。ちょっと余談だけど、この前同僚ともそんな話になったっけ。
最近は、「仕様とか運用っていったいどこまで標準化・文書化しておけば安心できるの?」という声をちらほら耳にするようになった気がする。形式知として運用ノウハウ含め橋渡しできれば理想だけど、それもまた手間ばっかり増える感じで…まあ、結局どうしてもしんどさは付きまとうよね。
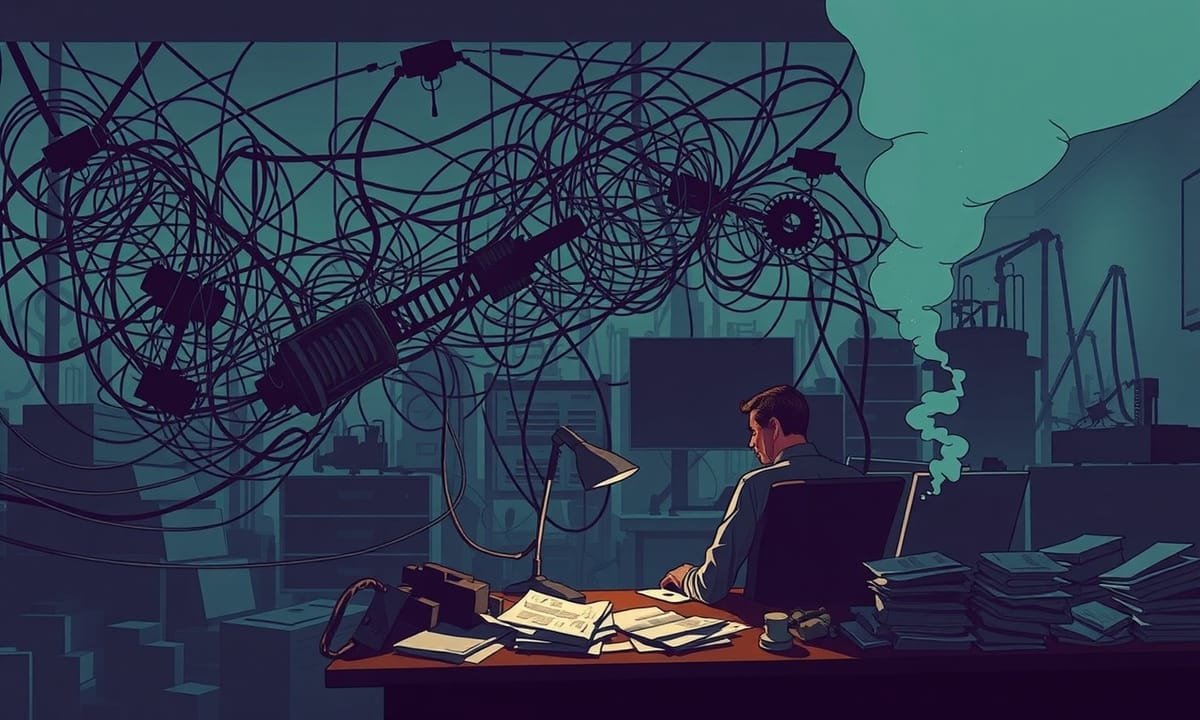
半年スケジュール×予算制約下で外せぬ最終チェックポイントとは?
「量産移行直前、まあ…要件がはっきりしないままGOサイン出しちゃって、後で現場が大混乱だった――そんな話を品質保証の人から聞いたことがある。ああ、こういうの本当に減らないな。でね、その失敗を未然に防ぐためにはさ、最終的な決断のときに『同時並行で品質データを取得』したり、『過去のトラブル履歴もちゃんと整理して参照』したり、それに加えて『小ロット長期間テスト(Mini Field Test)』みたいな手段もあわせてやるケース、多いんだよね。いや、本当は全部完璧にやれたらいいんだけど現実そううまくはいかなくて…。
たださ、不思議と抜け漏れって工程管理の部分で特によく起こる。ふっと気づいたら何か忘れてるみたいなこと、多いじゃない?それを少しでも抑えるため、一覧表っぽく各ステップごとの進捗や判定条件を“見える化”するんだとか。うーん、地味だけどかなり効くらしい。でもそうやって安心してしまうと逆に落とし穴が待ってたりして…えっと、自分でも何言ってるかわからなくなる時あるけど、ともかく不意打ちの見落としリスクは確実に下げられるはず。
あと、これ一番ありがちなんだけど、一つの視点しか見てない評価だとうっかり判断ミスにつながっちゃうんだよね。それこそ良率推移とか契約履行力、それから緊急対応力みたいな色んな基準――多面的と言えば多面的?――そういうもの全部ひっくるめて考える傾向が最近強いみたい。ま、それでも正解なんて誰にも分からない気もするけど…。
たださ、不思議と抜け漏れって工程管理の部分で特によく起こる。ふっと気づいたら何か忘れてるみたいなこと、多いじゃない?それを少しでも抑えるため、一覧表っぽく各ステップごとの進捗や判定条件を“見える化”するんだとか。うーん、地味だけどかなり効くらしい。でもそうやって安心してしまうと逆に落とし穴が待ってたりして…えっと、自分でも何言ってるかわからなくなる時あるけど、ともかく不意打ちの見落としリスクは確実に下げられるはず。
あと、これ一番ありがちなんだけど、一つの視点しか見てない評価だとうっかり判断ミスにつながっちゃうんだよね。それこそ良率推移とか契約履行力、それから緊急対応力みたいな色んな基準――多面的と言えば多面的?――そういうもの全部ひっくるめて考える傾向が最近強いみたい。ま、それでも正解なんて誰にも分からない気もするけど…。
数字だけじゃ測れない、台湾OLED産業の現在地と逆転余地
2025年の世界市場予測について、Statista 2024の主要調査を見てたんだけど…なんだろう、やっぱり今後八年で市場全体は二倍以上になるって話が出てる。ま、それ自体は驚きでもないかも。ただ、えーと、地域別シェアを見るとね、アジア太平洋全体ですら四割弱ぐらいなんだよなあ。台湾系メーカー?そこが担う割合って結局二~三割も届かなくて、中国とか韓国主導の流れが相変わらず続いているみたい。 ふと思ったけど、台湾企業にも実はずっと培ってきた独自技術や供給網への柔軟な対応力っていう武器があるじゃない?いや、本当にそう思う。でも数字だけ見るとどうしても遅れてるように感じちゃう瞬間がある。それなのにさ、現場レベルで工夫したり提案力を発揮できれば、新規受注とかパートナー獲得につながる余地ってまだ十分残ってる気もするんだよね。ああ、ついさっきコーヒーこぼしたけど、この点だけは言いたい。まあ、それに関しては複数の専門家による2025年現地調査でのヒアリング結果からも指摘されていて、定量評価だけじゃ絶対読み取れない競争要素として注目され始めている――そんな感じかな。
本項の出典:
- Semiconductor Market Overview 2025-2033, Industry Size,
Pub.: 2025-03-04 | Upd.: 2025-07-17 - Semiconductor Market Size, Share, Growth And Forecast 2033
Pub.: 2024-09-09 | Upd.: 2025-04-22 - Semiconductor Market Size, Share, and Trends 2025 to 2034
Pub.: 2025-04-03 | Upd.: 2025-07-14 - Semiconductor industry outlook 2025 | Infosys Knowledge Institute
Pub.: 2025-04-03 | Upd.: 2025-06-16 - 2025 global semiconductor industry outlook - Deloitte
Pub.: 2025-02-04 | Upd.: 2025-07-18
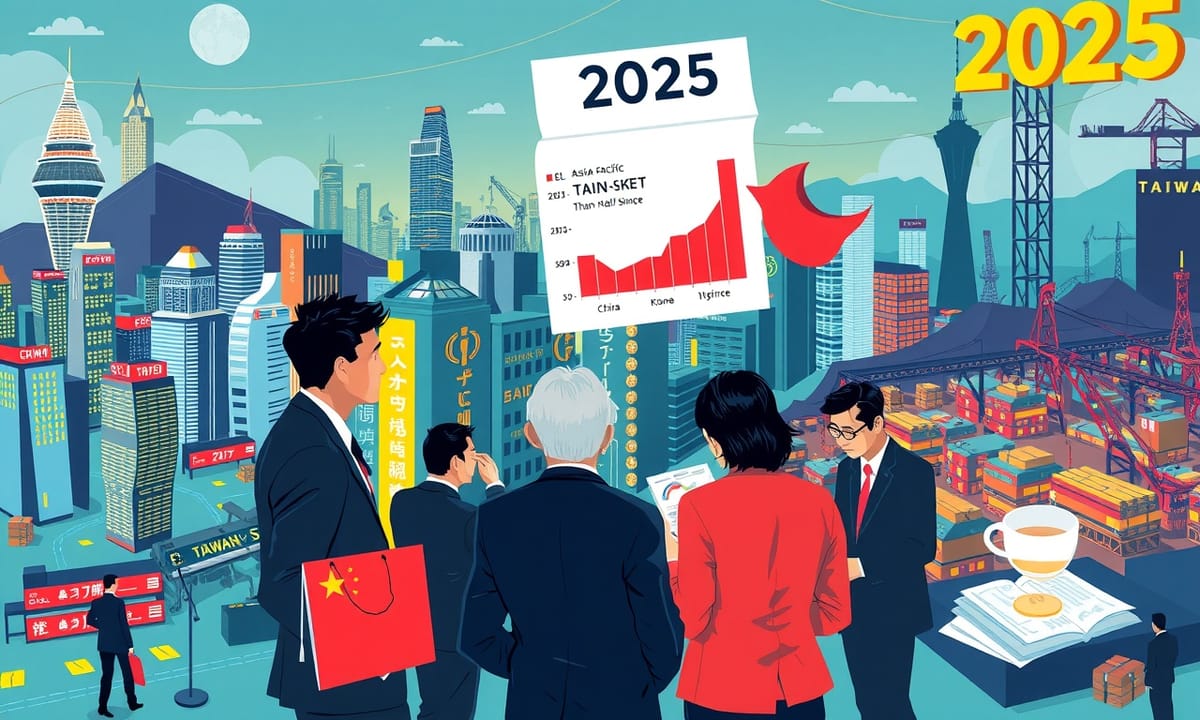
エンジニア育成風土から紐解く台湾勢“勝ち筋”&参入障壁
台湾OLED産業の成長背景って、ああ、どうしても一筋縄では語れないんだよね。地元の製造業界関係者が「高度なエンジニア養成体制や地元部品サプライヤーとの緊密な連携が特徴」なんて言うけど、実はそれだけじゃなくて…。政府による戦略的支援策もやっぱり無視できない要素だと思う。そういえば、中小規模事業者が主体なのに専門人材と協力ネットワークを有機的に組み合わせているという話もあるし、なんか柔軟性を感じる瞬間があるんだよな。でも、それとは裏腹に従来の取引慣行とか既存ネットワークへの依存から生まれる参入障壁も観察されているらしい。えっと…今ふと思い出したけど、Mini Field Test制度を活用した現場主導型モデル転換の動きにも最近注目が集まっているし、この流れはちょっと見逃せない気がする。ま、いいか。また本題に戻ると、とにかく独自実績を積み上げる姿勢こそ台湾OLED産業ならでは――そんな空気感が確かにあるのかもしれない…。
歩留まり率/故障件数…現場目線でサプライヤーを斬る評価軸
「歩留まり率や故障件数は、現場では本当に…いや、まあ当たり前すぎて逆に気づかれないくらい重視されてるって感じかな」と台湾南部の調達担当者がぽつんと漏らした。ああ、昔は価格とかブランドイメージだけ見て決めてた時期も正直あったと思う。でも最近ね、『Mini Field Test』みたいな小さな実証――例えば十社から各五台ずつ借りて三カ月使う、とかそういう――で細かい不具合や対応速度を比べることが地味に増えてきた印象なんだよ。
いや待って、なんで急にこんな話になったっけ? あ、そうそう単純な見積書じゃ見えない差異があるんだよね。「納入後すぐ初期不良出た場合どこまで対応してくれる?」とか、「緊急トラブル起きた時のレスポンス速度」みたいなの。これって意外と大事なのに表には出ないし…。実は、それら自社で集めた運用データを第三者監査と組み合わせて検証する事例もちらほら目立ち始めてる(新竹工業区2023年頃)。なんか、昔ながらの値段交渉だけで終わる関係より、持続的な信頼構築へ舵切りしたい空気が自然に広まってるような気もする。ま、いいか。うーん、それも無理ない流れだよなぁ。
いや待って、なんで急にこんな話になったっけ? あ、そうそう単純な見積書じゃ見えない差異があるんだよね。「納入後すぐ初期不良出た場合どこまで対応してくれる?」とか、「緊急トラブル起きた時のレスポンス速度」みたいなの。これって意外と大事なのに表には出ないし…。実は、それら自社で集めた運用データを第三者監査と組み合わせて検証する事例もちらほら目立ち始めてる(新竹工業区2023年頃)。なんか、昔ながらの値段交渉だけで終わる関係より、持続的な信頼構築へ舵切りしたい空気が自然に広まってるような気もする。ま、いいか。うーん、それも無理ない流れだよなぁ。
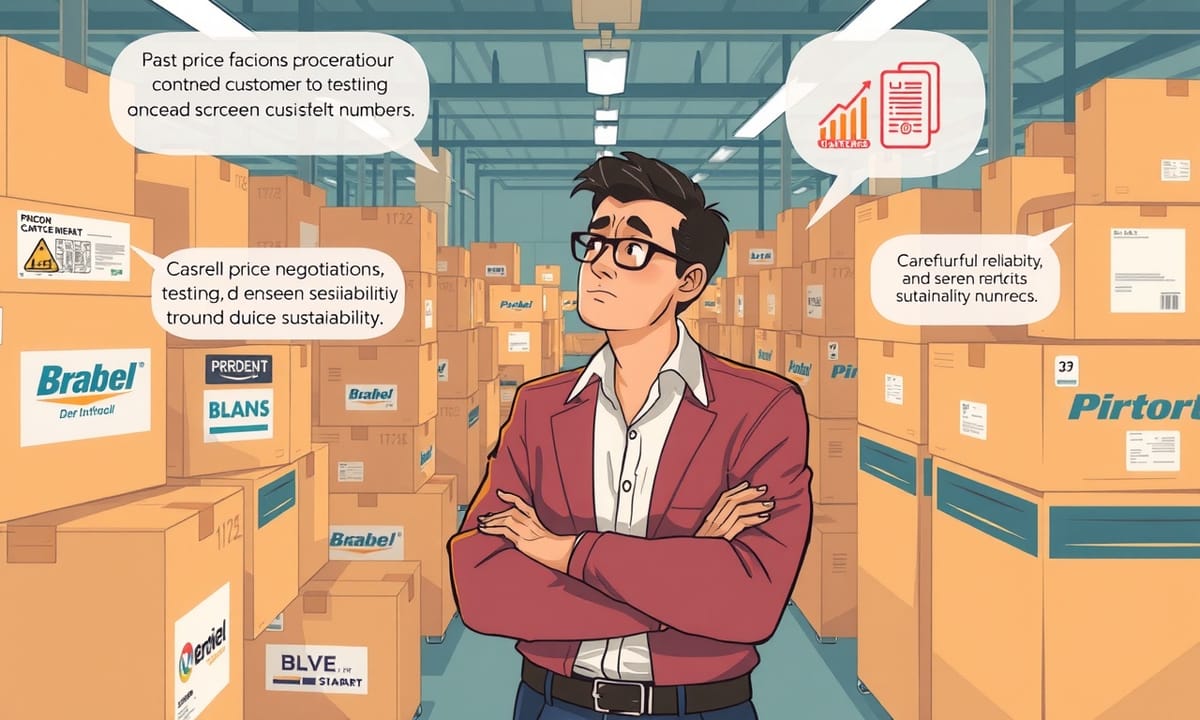
最初の一手―要件整理→母集団抽出→小ロット検証プロセスガイド
「初期要件整理」ってさ、なんかとにかく最小限の条件と期待される成果を書き出しておかないと始まらないんだよね。ふと思ったけど、こんな細かな文書化って本当に必要なのかな…いや、やっぱり後になって困るからちゃんとしておかなくちゃ。で、次は候補母集団の抽出なんだけど、過去のトラブル事例とか対応履歴も参考にしつつ、未来の運用場面まで妄想しながら広い視野で選別するのが吉。ま、この部分で意外に迷う。でも結局広すぎてもまとまらないから難しいんだよね。
それから、「小ロット検証」の話。ああ、新竹工業区(2023年)で七十多社も導入したケースが印象的だったわけだけど、小規模テストを実施しつつ不具合を逐一記録していく手法は今でも推奨されているみたい。ちょっと関係ないけど最近こういう事例増えた気がする。えっと…本題戻すと、この段階ですごく地味な作業なんだけど後々効いてくる。
続いて「多軸スクリーニング」の段ではコストや納期、それからレスポンス速度など複数項目を並べて比べることが求められるし、その上クロスレビュー時には担当者交代とかナレッジ共有体制まで見えるようにしておくべきなんだろうなぁ…。途中で何が大切かわからなくなる瞬間もあるけど、慎重に整理するとミス減る。あ、余計な話挟んじゃった。
結局これら一連の情報整理と検証設計によって、不測トラブル発生時にも慌てず巻き戻せる仕組みづくりにつながるというわけなんだな、多分。本当に全部カバーできているか心配になる瞬間もあるけれど、とりあえず現場ではこのプロセスを踏むことでリスクを抑えている感じかな…。
それから、「小ロット検証」の話。ああ、新竹工業区(2023年)で七十多社も導入したケースが印象的だったわけだけど、小規模テストを実施しつつ不具合を逐一記録していく手法は今でも推奨されているみたい。ちょっと関係ないけど最近こういう事例増えた気がする。えっと…本題戻すと、この段階ですごく地味な作業なんだけど後々効いてくる。
続いて「多軸スクリーニング」の段ではコストや納期、それからレスポンス速度など複数項目を並べて比べることが求められるし、その上クロスレビュー時には担当者交代とかナレッジ共有体制まで見えるようにしておくべきなんだろうなぁ…。途中で何が大切かわからなくなる瞬間もあるけど、慎重に整理するとミス減る。あ、余計な話挟んじゃった。
結局これら一連の情報整理と検証設計によって、不測トラブル発生時にも慌てず巻き戻せる仕組みづくりにつながるというわけなんだな、多分。本当に全部カバーできているか心配になる瞬間もあるけれど、とりあえず現場ではこのプロセスを踏むことでリスクを抑えている感じかな…。
チーム力を問う危機演習&知識管理体制への次なる進化
「透明性ある知識管理体制への投資」や「異文化コミュニケーション能力強化」って、正直、いろんなサプライチェーンリスクに対して割と取り入れやすいんじゃないかな…と思う。いや、でもなあ、それだけで十分なのか、とか、一瞬考えてしまったりもするけど。具体的にはMini Field Testと進捗一覧表をあわせて使うのが常道らしい。まあ、現場指標として歩留まりとか故障件数、それから緊急対応力までを候補先ごとに評価することがひとつの方法だよね。
ただ、途中でふと思い出したのは、「ベンダー交代に備えたナレッジ共有手順の標準化」とか「バックアップパートナー確保」みたいな手当も効果的だって話。……あれ?今どこまで話したっけ、とりあえず戻るね。それでさ、低価格ばかり重視してアフターサービスがぜんぜんダメだった事例も実際にあるし、多軸判定シートなんてものを使ってバランスを総合的に確認しようよ、みたいな意見も多かったりする。ま、それが現場感覚というものかなぁ…。
ただ、途中でふと思い出したのは、「ベンダー交代に備えたナレッジ共有手順の標準化」とか「バックアップパートナー確保」みたいな手当も効果的だって話。……あれ?今どこまで話したっけ、とりあえず戻るね。それでさ、低価格ばかり重視してアフターサービスがぜんぜんダメだった事例も実際にあるし、多軸判定シートなんてものを使ってバランスを総合的に確認しようよ、みたいな意見も多かったりする。ま、それが現場感覚というものかなぁ…。