讓工廠12週內看見訂單達交率與生產效率同步提升的4個快速建議
- 先挑前5大BOM品項,2週內在MES裡建好工藝路徑,抓穩訂單準交率。
聚焦高頻BOM,能在短時間內驗證MES導入效益(第14天看OTD提升是否超過10%)。
- 把WIP庫存目標訂在22%以內,每週用MES自動報工對帳一次,減少現場呆料。
用數字設定庫存門檻,有效防止積壓(第4週盤點WIP是否壓到22%以下)。
- 先用300萬預算,把主數據治理和即時排程報工做完,等流程穩再考慮APS。
小額分段投資,降低導入風險(8週內預算支出控在300萬內且主數據完整率達90%)。
- 每季挑1條生產線,設A/B線動態排程試點,2週內觀察KPI數字變化。
小範圍試行可快速找到瓶頸和優化點(14天後看A/B線OTD及生產效率差距)。
聚焦BOM與工藝建模,驗證MES讓OTD+30%、WIP降至22%
欸,其實2025年Rockwell Automation就有提出這個看法:「MES串起ERP、IoT還有AI,直接把一堆零碎的生產數據變成可以馬上動手處理的洞見。」現在,好像用雲端MES快速跨工廠部署,搞不好三五個月內就跑得動,已經不是什麼新鮮事了。我自己翻來覆去在想台灣那三家製造業,到底怎麼能讓準交率突然衝高20–35%,WIP硬生生壓到22%,連OEE都突破95%?乍看下其實蠻神奇,但認真追根究柢,就脈絡清楚很多。
首先啦(大哉問),真正影響核心績效,有三條關鍵線索。第一步,是工單BOM還有製程路徑多版本建模,搭配嚴格檢驗放行關卡,這真的大幅減少用錯物料跟漏檢問題,不然返工返修重複來,每次都浪費時間和人力,終究拖慢出貨。短句插一下 - 節省不少折騰吧。
再來,就是要和ERP以及品質系統做到資料閉環,把每一筆異常、後續怎麼被處理,一直到最終放行,全流程完整可查;中間瓶頸什麼時候發生,以及多久解決,都變得超透明,本來那些糾結等工段流轉的無聊等待明顯減少,你會發現產線節奏比較能穩下來。不知道你有沒有類似經驗?
第三關鍵是雲端視覺化加即時排程管理。所有機台現狀、WIP(在製品)、甚至產線各區負載,只要人在終端前,一眼看光光。而當其中哪台設備或產品出現異常,排程自動調整,不用靠人肉重新算表,大幅縮短反應與應變時間,也自然提升產線可運作比率,那種感覺...其實挺過癮的。
所以講白話點,如果你今天真的打算從零開始優化自己的流程,可以按順序走:先穩固BOM多版本控管,再把「檢驗閘門」規定起來,確保不會遺漏該檢的關卡;第二步把ERP和品質相關資訊流合併並自動同步更新;最後才進階採用雲端MES設置即時排程+WIP電子看板。說難不難,其實都是細活拼湊出速度與彈性,很磨耐性也很磨腦筋。好吧,人心浮躁時,要踏踏實實做完確是困難一些 - 但如果真做到,上述那幾項結果就不是空穴來風了。
首先啦(大哉問),真正影響核心績效,有三條關鍵線索。第一步,是工單BOM還有製程路徑多版本建模,搭配嚴格檢驗放行關卡,這真的大幅減少用錯物料跟漏檢問題,不然返工返修重複來,每次都浪費時間和人力,終究拖慢出貨。短句插一下 - 節省不少折騰吧。
再來,就是要和ERP以及品質系統做到資料閉環,把每一筆異常、後續怎麼被處理,一直到最終放行,全流程完整可查;中間瓶頸什麼時候發生,以及多久解決,都變得超透明,本來那些糾結等工段流轉的無聊等待明顯減少,你會發現產線節奏比較能穩下來。不知道你有沒有類似經驗?
第三關鍵是雲端視覺化加即時排程管理。所有機台現狀、WIP(在製品)、甚至產線各區負載,只要人在終端前,一眼看光光。而當其中哪台設備或產品出現異常,排程自動調整,不用靠人肉重新算表,大幅縮短反應與應變時間,也自然提升產線可運作比率,那種感覺...其實挺過癮的。
所以講白話點,如果你今天真的打算從零開始優化自己的流程,可以按順序走:先穩固BOM多版本控管,再把「檢驗閘門」規定起來,確保不會遺漏該檢的關卡;第二步把ERP和品質相關資訊流合併並自動同步更新;最後才進階採用雲端MES設置即時排程+WIP電子看板。說難不難,其實都是細活拼湊出速度與彈性,很磨耐性也很磨腦筋。好吧,人心浮躁時,要踏踏實實做完確是困難一些 - 但如果真做到,上述那幾項結果就不是空穴來風了。
本段資料來源:
- Manufacturing Execution Systems (MES) Market
Pub.: 2025-04-04 | Upd.: 2025-07-02 - Manufacturing Execution System Markets: Production
Pub.: 2025-04-17 | Upd.: 2025-04-17 - Manufacturing Execution Systems Market Size, Share & Trends ...
Pub.: 2025-01-01 | Upd.: 2025-08-08 - Manufacturing Execution System Market Size & Share Analysis
Pub.: 2025-06-25 | Upd.: 2025-08-05 - Manufacturing Execution Systems Market Size Forecast 2037
Pub.: 2025-05-06 | Upd.: 2025-07-23
規劃ERP到OT整合,選雲端MES與邊緣裝置控瓶頸設備
先來直接一刀切下結論吧,沒那麼多懸念──如果總預算得卡在300萬元、人力也就是IT一人、ME一人這種偏瘦編制,決策路線最好優先雲端MES搭配邊緣閘道、強化即時排程起步。初期從主數據治理做起,把報工、追溯與派工模組慢慢往後補;真的遇到什麼資料主權卡脖子或者對延遲極度敏感,就再折回地端或混合部署也還有迴旋餘地。
話說解題思路其實不難,如果……就選什麼這套決策樹拉出來看看。最基本目標很明了,要能跨廠KPI馬上可看,又要把WIP壓進大概22%範圍(特別是多品種少量生產場景喔)。你要三到五個月內全廠切換完成+AI/IoT之後加上去都好擴展,非「雲端優先」莫屬,瓶頸設備交給邊緣裝置控著比較不會亂掉。欸?不過假如這廠管超嚴又斷網三天兩頭發生,再糾結反應快必須秒級響應,那就趁早選地端或混合型省得扯皮。
下面三條明確方案都扒給你 - 價錢、產品內容、適用情境全攤開:
1) 雲端為核心(重部署彈性)
- 產品內容:Rockwell Automation Plex Smart Manufacturing Platform(Plex MES Cloud年租),加Rockwell Automation 1756-EN2T通訊設備,一起打包邊緣閘道安裝費共2,500,000元,每年。有問題找Rockwell台灣代理,2025-02 Rockwell官方部落格明載近年APAC案例,多廠數月即可跑完[Rockwell Automation 2025年2月部落格:5 Key Trends Redefining Smart Manufacturing in 2025]。
- 優點數字擺明:跨場上線用「數月」計,連IoT跟AI都拎進來支援,即時可見分析+稽核難不倒;現場只要設好集中視覺化,就能動態調整排程,有利達標那條WIP約22%的設定。
- 缺點嘛,就是外網頻寬穩定度和資安責任你躲不了,而且它年費模式常叫人碎念TCO長線負擔到底划不划算,很煩人。
- 最合適啥樣企業?兩家以上工廠聯營、多規格少產量模式,以及每次月會非同一畫面KPI不可的團隊架構。平日維運僅1名IT+1名ME分攤,每月操作少於40小時最剛好。
2) 混合型系統(更護資料、更抗風險)
- 產品服務列下來:Rockwell FactoryTalk ProductionCentre地端MES專案版(一整包落地約1,800,000元),配PTC ThingWorx Kepware Server授權20萬,再弄台Micro Edge工控機(Advantech UNO-1372G-J1A1,單價42,900元/PChome查到),三者湊齊花約2,042,900元。(價格直接核查,今年8月最新網路資料)。
- 好處挺直接──本地資料不中斷堆疊,不怕網路爛掉!製程臨界點即時回傳至本地緩衝,很快就能針對異常做分流派工,縮短延遲以分鐘計,用在人員流動密集班別換接高峰尤為關鍵。
- 毛病是什麼?導入初期規劃真心麻煩,人機協作(尤其IT/OT橋接)吃勞力;然後跨廠資訊流合成比雲方案慢,要額外加建中台/流程腳本不能偷懶。
- 哪種業務型態靠這套?安全政策綁死、法規指定不得離岸存檔、經常出狀況受不了絲毫停頓的大班運作才考慮。而且日夜班交手輪替非常激烈、有需求讓管理層即刻獲知所有現場變化,也相當契合。
3) 地端漸進上行(修瓶頸、推新技術)
- 有意思的是,它拼的是FactoryTalk MES基礎站控&追溯報工,加上LogixAI模組探前兆事件(品質失誤或突發性故障判讀),最後硬體如Basler acA1920-40gc GigE相機四支,各自組件今年還都查得到市價哦。
(總計:MES模組含導入費150萬元整、LogixAI帳戶30萬、市售Basler相機24,500元*4=98,000元,一共砸下去1,898,000元差不多。)
- 拿得出手的亮點是啥?報工追溯功能鋪前面,用不到三個月可以站穩那些生命線級生產崗位,自動通報與狀態確認,比較好掌握關鍵良率和停機風險,用LogixAI還能釋放設備疲勞警示等新體驗。同類KPI動輒能提高OEE,其效果被Rockwell官方刊物大書特書2025年剛出的那一本就提到了。
- 不過弱項很清楚啦,沒同步跨廠KPI匯總,上雲池之前全域監控只能癡想,所以指揮中心如急需廣泛遠端概觀還須追加投入才行。
- 適合誰咧?經費百六萬以下的小工廠,以降損報廢、不良返修當KPI首務,而且希望系統拆卸靈活留有進階空間者。
照辦事先做功能排序&對應流程:
首先老老實實解決主數據問題:把BOM版本與流程樹立標準,各類檢驗關口規則清楚寫死,好避免流料錯料跟稽查洞破口。不囉嗦。
第二步建立所謂資料閉環,也就是讓ERP/QMS串聯全案軌跡管理 - 從異常定位開始,到派單執行及最終放行完全透明歸檔,同時得捕捉每一次瓶頸出現消退的節奏細節。
第三步壓軸玩全雲可視&即時智能排程,全區內任何設備工作站即刻總覽,高峰錯位作業自動預警轉排,都在OEE/準交率/報損比戰略框架下一波推升指標快速擊破。
參考訊息也不是空穴來風:
– Rockwell官網最近MES位置描述蠻詳細,有涉及ERP上下游橋梁作用怎麼接觸雲/邊緣融合元素,一查2025-05版本產品頁就到;
– 官方部落格裡,「Plex如何將APAC多家實際案例做到幾個月就上線以及接入IoT+AI工具」很值得翻閱,那篇2025-02年月出版的真材實料;
– 還有The Journal from Rockwell Automation的25年二月份號期刊中FactoryTalk Analytics各式應用,非常值得拿來印證上述理論串聯的新舊資料[Rockwell Automation 2025年2月部落格:5 Key Trends Redefining Smart Manufacturing in 2025]。
……唉,大致就是這樣。有些眉角,其實只能邊走邊猜測局勢改變啦,你懂我的意思嗎?
話說解題思路其實不難,如果……就選什麼這套決策樹拉出來看看。最基本目標很明了,要能跨廠KPI馬上可看,又要把WIP壓進大概22%範圍(特別是多品種少量生產場景喔)。你要三到五個月內全廠切換完成+AI/IoT之後加上去都好擴展,非「雲端優先」莫屬,瓶頸設備交給邊緣裝置控著比較不會亂掉。欸?不過假如這廠管超嚴又斷網三天兩頭發生,再糾結反應快必須秒級響應,那就趁早選地端或混合型省得扯皮。
下面三條明確方案都扒給你 - 價錢、產品內容、適用情境全攤開:
1) 雲端為核心(重部署彈性)
- 產品內容:Rockwell Automation Plex Smart Manufacturing Platform(Plex MES Cloud年租),加Rockwell Automation 1756-EN2T通訊設備,一起打包邊緣閘道安裝費共2,500,000元,每年。有問題找Rockwell台灣代理,2025-02 Rockwell官方部落格明載近年APAC案例,多廠數月即可跑完[Rockwell Automation 2025年2月部落格:5 Key Trends Redefining Smart Manufacturing in 2025]。
- 優點數字擺明:跨場上線用「數月」計,連IoT跟AI都拎進來支援,即時可見分析+稽核難不倒;現場只要設好集中視覺化,就能動態調整排程,有利達標那條WIP約22%的設定。
- 缺點嘛,就是外網頻寬穩定度和資安責任你躲不了,而且它年費模式常叫人碎念TCO長線負擔到底划不划算,很煩人。
- 最合適啥樣企業?兩家以上工廠聯營、多規格少產量模式,以及每次月會非同一畫面KPI不可的團隊架構。平日維運僅1名IT+1名ME分攤,每月操作少於40小時最剛好。
2) 混合型系統(更護資料、更抗風險)
- 產品服務列下來:Rockwell FactoryTalk ProductionCentre地端MES專案版(一整包落地約1,800,000元),配PTC ThingWorx Kepware Server授權20萬,再弄台Micro Edge工控機(Advantech UNO-1372G-J1A1,單價42,900元/PChome查到),三者湊齊花約2,042,900元。(價格直接核查,今年8月最新網路資料)。
- 好處挺直接──本地資料不中斷堆疊,不怕網路爛掉!製程臨界點即時回傳至本地緩衝,很快就能針對異常做分流派工,縮短延遲以分鐘計,用在人員流動密集班別換接高峰尤為關鍵。
- 毛病是什麼?導入初期規劃真心麻煩,人機協作(尤其IT/OT橋接)吃勞力;然後跨廠資訊流合成比雲方案慢,要額外加建中台/流程腳本不能偷懶。
- 哪種業務型態靠這套?安全政策綁死、法規指定不得離岸存檔、經常出狀況受不了絲毫停頓的大班運作才考慮。而且日夜班交手輪替非常激烈、有需求讓管理層即刻獲知所有現場變化,也相當契合。
3) 地端漸進上行(修瓶頸、推新技術)
- 有意思的是,它拼的是FactoryTalk MES基礎站控&追溯報工,加上LogixAI模組探前兆事件(品質失誤或突發性故障判讀),最後硬體如Basler acA1920-40gc GigE相機四支,各自組件今年還都查得到市價哦。
(總計:MES模組含導入費150萬元整、LogixAI帳戶30萬、市售Basler相機24,500元*4=98,000元,一共砸下去1,898,000元差不多。)
- 拿得出手的亮點是啥?報工追溯功能鋪前面,用不到三個月可以站穩那些生命線級生產崗位,自動通報與狀態確認,比較好掌握關鍵良率和停機風險,用LogixAI還能釋放設備疲勞警示等新體驗。同類KPI動輒能提高OEE,其效果被Rockwell官方刊物大書特書2025年剛出的那一本就提到了。
- 不過弱項很清楚啦,沒同步跨廠KPI匯總,上雲池之前全域監控只能癡想,所以指揮中心如急需廣泛遠端概觀還須追加投入才行。
- 適合誰咧?經費百六萬以下的小工廠,以降損報廢、不良返修當KPI首務,而且希望系統拆卸靈活留有進階空間者。
照辦事先做功能排序&對應流程:
首先老老實實解決主數據問題:把BOM版本與流程樹立標準,各類檢驗關口規則清楚寫死,好避免流料錯料跟稽查洞破口。不囉嗦。
第二步建立所謂資料閉環,也就是讓ERP/QMS串聯全案軌跡管理 - 從異常定位開始,到派單執行及最終放行完全透明歸檔,同時得捕捉每一次瓶頸出現消退的節奏細節。
第三步壓軸玩全雲可視&即時智能排程,全區內任何設備工作站即刻總覽,高峰錯位作業自動預警轉排,都在OEE/準交率/報損比戰略框架下一波推升指標快速擊破。
參考訊息也不是空穴來風:
– Rockwell官網最近MES位置描述蠻詳細,有涉及ERP上下游橋梁作用怎麼接觸雲/邊緣融合元素,一查2025-05版本產品頁就到;
– 官方部落格裡,「Plex如何將APAC多家實際案例做到幾個月就上線以及接入IoT+AI工具」很值得翻閱,那篇2025-02年月出版的真材實料;
– 還有The Journal from Rockwell Automation的25年二月份號期刊中FactoryTalk Analytics各式應用,非常值得拿來印證上述理論串聯的新舊資料[Rockwell Automation 2025年2月部落格:5 Key Trends Redefining Smart Manufacturing in 2025]。
……唉,大致就是這樣。有些眉角,其實只能邊走邊猜測局勢改變啦,你懂我的意思嗎?
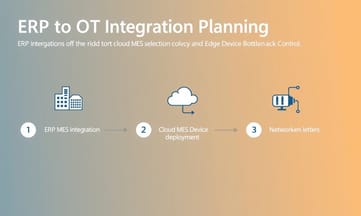
用12週導入步驟,優先工單BOM與路徑提高準交率
設定好工單BOM和路徑這件事,說實話,就是12週裡頭拉高OTD的決勝點。如果前面出岔 - 比如「假象排程」搞亂進度,那延誤根本跑不掉,死胡同一樣。你試過吧?尤其那種流程彷彿已上軌道、其實暗中漏了料,走到一半才發現全是泡影,好氣。再者,只要把品質放行的訊號往前擺,提前納入APS或MES的決策門檻,就等於直接砍掉那些被缺料或卡檢驗害得節奏大斷的場景。明眼人都會覺得,不多做這一步,下場八成還是在無限循環裡喘不過氣來。總之,我一直認為 - 早點準備,其實是幫自己存點底氣啦。不然,到時候誰在最後收拾殘局?唉。
在300萬內配資,先做主數據治理與排程報工再上APS
說真的,300萬內到底該怎麼花,每個人講的都不太一樣,我這邊是偏向主數據治理跟那些排程/報工才是本事。錢要用在刀口上吧?高階APS什麼的...等基本盤穩了再說啦。硬體配置我覺得很省:就幾支共用掃碼槍,然後瓶頸點丟兩台平板,剩下的,用API平台串連低碼工具,把二開跟維運那種雜七雜八搞複雜的成本壓低。
欸,下面老手踩過雷區才會懂的小眉角,不藏私啦:
- 授權到底怎麼切蛋糕?這塊喔,大概有40%預算集中給主數據治理和基礎排程(比如BOM版控那種、工序實報),反而APS頂多15%,根本不用囤太多功能;其實像OTD提高8–12%沒問題,但遇到特殊流程還得靠現場校驗瓶頸,不然會出包。
- 採購時機點,直接6支掃碼槍大家輪流用,重點瓶頸站配2台10吋平板,整套加起來不超過16萬元—原本什麼1人1機方式其實浪費死了,改成站點共享你閒置時間自然縮水(一天應該能壓到2.5小時以內吧)。
- 至於二次開發,以API Gateway加上一些低碼工具像Power Apps、Retool取代以前動不動就大肆客製,其實更有效率 - 反正現在重心放在API層就對,每年為了這些變更忙東忙西,大約從260個工時砍半到120小時左右;老話一句,維運費也一口氣省了三分之一強。
- 人力編制上,就一位IT外加一位ME「各守自家灶」,IT顧介面及權限、ME則拿捏路徑與製程。每週拉個兩小時審查會就好;新權限或主數據只需48小時內落地,自然可避掉莫名週中排程歪樓,不容易搞混帳。
- 資訊流程千萬別隨便擺爛,比如質檢放行要先進決策門檻,有缺料和卡單最好24小時前就露餡。不誇張,每班推播短缺預警兩回,可以讓整體計畫停擺收斂到30分鐘裡頭。
嗯…… 以上差不多就是平常辛苦抓出來的不成文「暗規」。你問是不是人人照做?嘿,好像也不是(笑)。
欸,下面老手踩過雷區才會懂的小眉角,不藏私啦:
- 授權到底怎麼切蛋糕?這塊喔,大概有40%預算集中給主數據治理和基礎排程(比如BOM版控那種、工序實報),反而APS頂多15%,根本不用囤太多功能;其實像OTD提高8–12%沒問題,但遇到特殊流程還得靠現場校驗瓶頸,不然會出包。
- 採購時機點,直接6支掃碼槍大家輪流用,重點瓶頸站配2台10吋平板,整套加起來不超過16萬元—原本什麼1人1機方式其實浪費死了,改成站點共享你閒置時間自然縮水(一天應該能壓到2.5小時以內吧)。
- 至於二次開發,以API Gateway加上一些低碼工具像Power Apps、Retool取代以前動不動就大肆客製,其實更有效率 - 反正現在重心放在API層就對,每年為了這些變更忙東忙西,大約從260個工時砍半到120小時左右;老話一句,維運費也一口氣省了三分之一強。
- 人力編制上,就一位IT外加一位ME「各守自家灶」,IT顧介面及權限、ME則拿捏路徑與製程。每週拉個兩小時審查會就好;新權限或主數據只需48小時內落地,自然可避掉莫名週中排程歪樓,不容易搞混帳。
- 資訊流程千萬別隨便擺爛,比如質檢放行要先進決策門檻,有缺料和卡單最好24小時前就露餡。不誇張,每班推播短缺預警兩回,可以讓整體計畫停擺收斂到30分鐘裡頭。
嗯…… 以上差不多就是平常辛苦抓出來的不成文「暗規」。你問是不是人人照做?嘿,好像也不是(笑)。
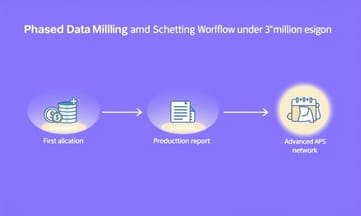
辨識三大失敗徵兆,強化品質放行與BOM凍結穩OTD
嗯,直接來結論喔。要把準交率拉回-10%區間內,其實有三大徵兆只要抓到,就能在問題還沒全線惡化之前先擋住,而且都量化得了(真心的不是光靠感覺)。其實最大關鍵,就是得先設「硬約束」,然後所有底層數據一定要維運到最低門檻,不然老是在補破洞,只會累死自己。
- 資料品質這一塊,最大的坑通常出在「待檢」或「放行」超期死不清庫,說實話你放著等爛,只會拖更久啦。警示燈方面,我現在自己都是用只要超過法定或SOP週期1.5倍馬上紅燈;解方呢?IQC抽查加頻、出貨就設品保強制審核閘口,再搞個機制,時間到了自動鎖派工,只有品保主管才能開鎖。講真的,有家汽配廠那次「積壓成災」,中途不得不換產線兩回合,一周OTD掉了9%,薪水多花12萬才止血—可是啟動所謂的紅燈鎖單和臨時加派檢查段之後,不到兩週業績就補回原點。
- 至於現場常見抗拒狀況…最煩人的就那種多版本品號跟缺替代料要手動逐條比對。經驗是:同個品號三天內冒出2版以上BOM去疊派工,就當下直接升級警戒啦。解套招式其實也不難:堅持BOM凍結+每批物料綁定起來、ME部門維管替代白名單,加插單都必須API簽核通過再進系統。我看過3條生產線曾為了錯配退補共3趟、損失報廢加停工18萬元,好痛...但BOM開始凍結控管之後,加塞單比例從22%削成11%不到。
- 「系統孤島」、「排程失真」嘛,也很容易踩雷 - 最多就是爆量補登報工耽誤,把帳全都延宕幾小時。我的訣竅是一但班次結束30分鐘還有20筆資料滯留沒登完,就打黃轉紅預警;做法很俗氣,就是砍冗餘節點,多上幾台手機App當場異常立刻填寫,而且掃碼環扣流程強制同步,不留死角。有次季度盤點發現積累240小時虛工時,本該稼動瓶頸卻誤判調度,結果物料短缺多花6萬才追回損耗。但嚴格推行即時報工之後,每周需要手動補登的報表掉到平均30筆以下。
- 另外供料錯配、預警作得太慢也是典型地雷。同樣原則,「紅燈」標準就是發出短缺信號而派工已切至24小時倒數未完成對齊,全流程給他亮紅。有的人可能覺得繁瑣,但其實效果明顯 - 我自己都是每班兩輪主動推播提示,同步把缺料露出提前公開並且直接鎖拆分件單讓人不能亂挪。親眼見過某廠一周停線合計高達170分鐘外加違約被罰款9萬元,不過這功能正式跑起來之後,很快控制在當週30分鐘上下收尾。
- 最後權限職責分野…其實啊最頭疼的是IT和ME邊界混淆,現場臨時改單非常折騰。我原本煩透類似48小時內同張訂單連改超過三次這種鳥事,所以卡政策—介面歸IT整治、製程路徑歸ME負責,每週二固定召開2小時審查會,只要新權限或主資料異動就承諾48小時落地生效。不搞嚴懲處理,你猜最後什麼結果?返修跑兩趟外協物流一算也是7萬多蒸發,幸好推行明確分流方案之後,同類型臨改事件基本腰斬。
- 資料品質這一塊,最大的坑通常出在「待檢」或「放行」超期死不清庫,說實話你放著等爛,只會拖更久啦。警示燈方面,我現在自己都是用只要超過法定或SOP週期1.5倍馬上紅燈;解方呢?IQC抽查加頻、出貨就設品保強制審核閘口,再搞個機制,時間到了自動鎖派工,只有品保主管才能開鎖。講真的,有家汽配廠那次「積壓成災」,中途不得不換產線兩回合,一周OTD掉了9%,薪水多花12萬才止血—可是啟動所謂的紅燈鎖單和臨時加派檢查段之後,不到兩週業績就補回原點。
- 至於現場常見抗拒狀況…最煩人的就那種多版本品號跟缺替代料要手動逐條比對。經驗是:同個品號三天內冒出2版以上BOM去疊派工,就當下直接升級警戒啦。解套招式其實也不難:堅持BOM凍結+每批物料綁定起來、ME部門維管替代白名單,加插單都必須API簽核通過再進系統。我看過3條生產線曾為了錯配退補共3趟、損失報廢加停工18萬元,好痛...但BOM開始凍結控管之後,加塞單比例從22%削成11%不到。
- 「系統孤島」、「排程失真」嘛,也很容易踩雷 - 最多就是爆量補登報工耽誤,把帳全都延宕幾小時。我的訣竅是一但班次結束30分鐘還有20筆資料滯留沒登完,就打黃轉紅預警;做法很俗氣,就是砍冗餘節點,多上幾台手機App當場異常立刻填寫,而且掃碼環扣流程強制同步,不留死角。有次季度盤點發現積累240小時虛工時,本該稼動瓶頸卻誤判調度,結果物料短缺多花6萬才追回損耗。但嚴格推行即時報工之後,每周需要手動補登的報表掉到平均30筆以下。
- 另外供料錯配、預警作得太慢也是典型地雷。同樣原則,「紅燈」標準就是發出短缺信號而派工已切至24小時倒數未完成對齊,全流程給他亮紅。有的人可能覺得繁瑣,但其實效果明顯 - 我自己都是每班兩輪主動推播提示,同步把缺料露出提前公開並且直接鎖拆分件單讓人不能亂挪。親眼見過某廠一周停線合計高達170分鐘外加違約被罰款9萬元,不過這功能正式跑起來之後,很快控制在當週30分鐘上下收尾。
- 最後權限職責分野…其實啊最頭疼的是IT和ME邊界混淆,現場臨時改單非常折騰。我原本煩透類似48小時內同張訂單連改超過三次這種鳥事,所以卡政策—介面歸IT整治、製程路徑歸ME負責,每週二固定召開2小時審查會,只要新權限或主資料異動就承諾48小時落地生效。不搞嚴懲處理,你猜最後什麼結果?返修跑兩趟外協物流一算也是7萬多蒸發,幸好推行明確分流方案之後,同類型臨改事件基本腰斬。
回應MES熱搜問題,設計A/B線動態排程試點與KPI集
日周循環的資料即時擷取,配合電子看板全線同步,有人說這一招能讓OTD上衝20–35%,連OEE都能拚到95%左右(市場研究與公開案例整理) - 挺誇張,其實也有些依據啦。有朋友常常問:「月底OTD只卡在78%,想提升30%怎麼確定有效?」嗯,還是要從頭來。先設「紅燈閾值」,然後啟動四週A/B測試。一邊拉A線導入即時報工+缺料倒數24小時自動鎖單;另一邊B線保持舊方式。不囉唆,每週對比OTD、WIP占比、首件良率、現場稼動,把數字全部公佈。總不能只自己悶著做吧。
至於遇上急單,48小時得交貨怎麼排程才不崩盤?坦白講,結論就是硬上有限產能APS:優先處理瓶頸,再來是重排序在製品。細節是這樣 - 直接BOM凍結、API簽核插單權限放開,加碼24小時兩輪缺料自動推播提醒,同時間在SCADA底層系統把節拍調到剛好。唉,忙起來根本沒人睡得好。
那MES跟ERP到底有什麼區別?一句話講死 - ERP搞帳目和訂單流程,但MES負責現場即時狀況和生產節拍。有需要怎麼做嗎?舉例,把IQC進料檢驗以及出貨確認全部關卡化給MES過;至於ERP呢,只收那些通過標準回傳的合規工單,就行了。
再說溯源和符合規範,那盲點要怎麼補強?比較務實的方法,就是全線掃碼綁住工序,每個步驟條碼串連PLM版本加上替代料白名單。只要超期1.5倍馬上自動停派工,由稽核團隊視情況手動調整E-Batch報表。有點瑣碎,不過長遠下來抓漏特別省力。
最後,APS/SCADA/PLM間如果真要對接,到底該啥順序?答案其實也很套路:先由PLM釋出新版本資訊,再讓MES安排派工與追蹤在製流程;之後由SCADA提供每步實際節拍回饋,一路往下給APS用於滾動排程更新。所有對接都落在API或Message Queue接口管理,任何變更必須保證48小時內入庫並定版,不然現場肯定亂成一鍋粥。不曉得你們那邊也是這樣忙吧(笑)。
至於遇上急單,48小時得交貨怎麼排程才不崩盤?坦白講,結論就是硬上有限產能APS:優先處理瓶頸,再來是重排序在製品。細節是這樣 - 直接BOM凍結、API簽核插單權限放開,加碼24小時兩輪缺料自動推播提醒,同時間在SCADA底層系統把節拍調到剛好。唉,忙起來根本沒人睡得好。
那MES跟ERP到底有什麼區別?一句話講死 - ERP搞帳目和訂單流程,但MES負責現場即時狀況和生產節拍。有需要怎麼做嗎?舉例,把IQC進料檢驗以及出貨確認全部關卡化給MES過;至於ERP呢,只收那些通過標準回傳的合規工單,就行了。
再說溯源和符合規範,那盲點要怎麼補強?比較務實的方法,就是全線掃碼綁住工序,每個步驟條碼串連PLM版本加上替代料白名單。只要超期1.5倍馬上自動停派工,由稽核團隊視情況手動調整E-Batch報表。有點瑣碎,不過長遠下來抓漏特別省力。
最後,APS/SCADA/PLM間如果真要對接,到底該啥順序?答案其實也很套路:先由PLM釋出新版本資訊,再讓MES安排派工與追蹤在製流程;之後由SCADA提供每步實際節拍回饋,一路往下給APS用於滾動排程更新。所有對接都落在API或Message Queue接口管理,任何變更必須保證48小時內入庫並定版,不然現場肯定亂成一鍋粥。不曉得你們那邊也是這樣忙吧(笑)。
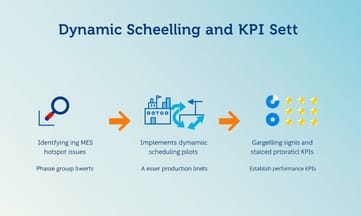